Predictive Maintenance: How To Optimize Laboratory Equipment Maintenance Schedules
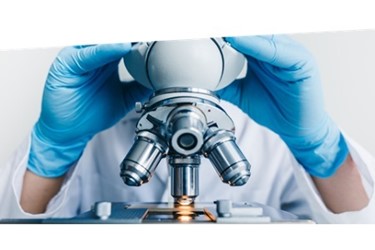
Laboratory workers and researchers must be cognizant that laboratory equipment can malfunction without adequate monitoring and regularly scheduled maintenance. Equipment typically does not undergo catastrophic failures without earlier indications or signs of underlying issues. The important factor is having the capabilities to detect any anomalies or deviations before the situation worsens to the point of total equipment failure.
Laboratory equipment failure can be both costly and devastating to operations. The high cost of repairing or replacing equipment is a major area of concern for laboratories. There are also potential losses in downtime when laboratory professionals cannot use the equipment to complete the necessary research to meet deadlines. Laboratory research technicians and scientists may also worry of the risk of invaluable research assets being disturbed or damaged while equipment is repaired or replaced.
Proactive vs. Reactive Maintenance
Having a proactive approach to scheduling laboratory equipment maintenance is important to avoid the potential risks often associated with reactive maintenance. As highlighted above, reactive maintenance can have many negative consequences for a company such as increased financial costs and downtime following an equipment failure. Unfortunately, many laboratories are not yet in the position to take advantage of the benefits involved with adopting proactive over reactive maintenance, which can cost exponentially more when properly evaluated.
Laboratory managers must ensure that proper standard operating procedures (SOPs) and maintenance schedules are in place for monitoring the functionality of laboratory devices and equipment in order to prevent any future failures from occurring. The best strategies are those that include comprehensive plans for preventive maintenance that are carefully adhered to. It is crucial for equipment to be properly installed, maintained, and calibrated to protect the integrity of the results that are obtained during research, as well as to avoid potential risks or injuries involving laboratory personnel. Preventive maintenance should include routine cleaning, monitoring and repairs, and timely replacement of any component that show signs of failure.
Going a step further, predictive maintenance is the prediction of future issues or failures before they happen, enabled by the careful monitoring of equipment, collection of historical data and development of predictive algorithms. By predicting potential problems, plans can be made for moving samples to properly functioning equipment while others are scheduled for maintenance. The appropriate procedures can be outlined for scheduling repairs or replacement of critical equipment. Maintenance plans can incorporate predictive results and ensure proper scheduling of equipment calibrations from the appropriate service vendors. This is another important component of facility management and should not be ignored.
The McKinsey Global Institute suggests that predictive maintenance will decrease costs between 10% and 40%, saving organizations in the long term. Downtime from equipment maintenance scheduling will also be cut in half, providing even more benefit.
Surveys of maintenance managers have found that the proactive approach to scheduling maintenance, calibration, or repairs is much more efficient and improves overall performance when compared with reactive maintenance. It can be very challenging to optimize laboratory research efficiencies when scheduling maintenance after equipment has totally failed. Proactive maintenance allows for better planning and can ensure that work is not disrupted when equipment is being repaired.
Facility management should include both proactive and predictive maintenance in order to safeguard equipment and the data obtained from such equipment. State-of-the-art facilities that aim to optimize best practices utilize device data monitoring to develop predictive models and ensure that all laboratory assets and equipment are properly functioning. Extended delays with reactive maintenance or waiting for repairs before it’s too late can lead to critical equipment failures and has shown billions of dollars in costs each year for facilities and operations teams. In comparison, the US Department of Energy indicated that predictive maintenance is cost-effective and leads to roughly 25% to 30% reduction in maintenance costs and a 70% to 75% decrease in equipment breakdowns. By adhering to proactive and predictive maintenance, in conjunction with improved SOPs and detailed documentation that provides clear guidelines on monitoring and maintenance schedules, organizations will begin to see great benefits in overall operations.
Data Analysis for Predictive Maintenance
Data analysis is a crucial aspect of an effective laboratory equipment monitoring program. Data analysis can often be difficult to understand and interpret, even more so if there are problems with equipment. Equipment can sometimes be purchased from original equipment manufacturers (OEMs) or through third-party sellers and resellers. This can pose a challenge to organizations when trying to collect and collate data from disparate systems.
XiltriX, a 24/7, autonomous, laboratory monitoring solution that collects data in real-time is an OEM agnostic software platform that works with a wide variety of laboratory equipment such as refrigerators, freezers, incubators, bioreactors, cryotanks, as well as backup generators, HVAC and BMS systems.
The XiltriX solution seamlessly acquires and analyzes data outputs from equipment to detect problems and provide predictive analytics well before any laboratory equipment may fail. Managers can instantly acknowledge any data anomalies and potential problems as soon as they arise. This constant monitoring of equipment helps ensure any catastrophic failure is avoided.
Utilizing XiltriX provides added layers of security and ensures that safeguards are in place for all laboratory equipment. Automated alarms and notifications will sound if any deviations outside of set parameters and specifications occur. Notifications can be sent through phone, email or text messages and the system can be accessed on any computer, tablet, or mobile device. Establishing escalation protocols allows the appropriate staff to be apprised of any potential problems and rectify any issues, saving time and money.