Process Validation: Optimizing Operational Excellence In Pharma And Medical Devices
By Jesper. M. Wagner, NIRAS
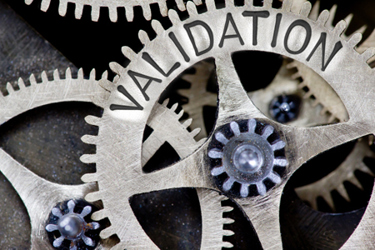
Process validation1,2 is often considered by management to be a costly regulatory formality — a necessary checkbox with little perceived business value. This mindset has caused some organizations to minimize validation investments, delegate the responsibility to underqualified personnel, or skip essential steps for short-term savings.
However, this perspective is increasingly outdated. While process validation is a regulatory requirement, its benefits extend far beyond compliance. When strategically implemented, validation evolves into a data-driven discipline that enhances operational efficiency, improves product quality, mitigates risk, and supports long-term financial performance.
In essence, process validation is a business enabler. It ensures the consistent production of high-quality products, minimizes deviations and rework, and facilitates smoother scale-up and market entry. By leveraging validation insights, companies can optimize production resources and accelerate revenue generation.
A compelling argument emerges when viewed through the lens of the cost of poor quality (COPQ).3,4,5 In pharmaceuticals, COPQ is estimated at 25%–40% of turnover and up to 40% of operating expenses, compared to just 4%–8% in quality-driven sectors like semiconductors.6 These figures highlight the cost of reactive quality management and the return on proactive validation.
This article reframes process validation as a strategic investment that, when integrated into business planning, delivers measurable outcomes in productivity, compliance, speed-to-market, and profitability. For management seeking growth, resilience, and competitive advantage, the key question is no longer “What does validation cost?” but rather, “What is the cost of poor quality?”
Process Validation As A Catalyst For Growth And Agility
From a growth perspective, process validation enables faster time-to-market. Validation provides critical insights into the relationship between process parameters and product quality, which proves invaluable during technology transfer and scale-up.
Based on firsthand experience, identifying key parameters early in a plastic molding process resulted in a fourfold reduction in the transition time from pilot to full-scale production.
In practical terms, process validation delivers:
- Efficient product launches: Validated processes streamline manufacturing and regulatory checkpoints.
- Accelerated global expansion: Facilities can leverage existing data for faster local approvals.
- Ongoing process optimization: Validation highlights critical parameters, enabling targeted, data-driven improvements.
Strategic Value: Efficiency, Speed, And Risk Reduction
Validation contributes directly to efficient and consistent production, with measurable business impact:
- Fewer deviations result in less downtime, rework, and investigations.
- Stronger process control improves equipment utilization and reduces the cost of goods.
- Faster scale-up shortens time-to-market and enables earlier revenue capture.
These gains are often reflected in overall equipment effectiveness (OEE), a key performance metric in manufacturing.6 A well-validated process enhances OEE by decreasing variability and ensuring stable, repeatable output.
Even minor improvements in yield or downtime can lead to substantial annual savings in high-volume environments.
In addition to operational gains, validation also mitigates regulatory risk. Poorly validated processes are a primary cause of regulatory action. A validated process decreases the likelihood of recalls and inspection observations, thereby strengthening trust with regulators and supply chain partners.7
The stakes are high: studies show that the cost of noncompliance can be three to 10 times greater than the cost of proper validation.8 This includes direct costs (recalls, rework) and indirect costs (market loss, reputational damage).
Quality Cost Reduction, Efficiency Gains, And ROI
One of the clearest benefits of validation is the reduction of quality issues such as nonconformities, deviations, and batch failures. This translates into fewer investigations, reduced material waste, and lower labor costs. In high-volume production, even minor reductions in scrap or rework can yield substantial savings.
Validated processes also enhance predictability, enabling accurate production planning, tighter inventory control, and reduced supply chain issues.7 This enhances resource utilization, reduces overproduction, and improves working capital efficiency.
From a financial standpoint, process validation is a value-generating activity, not a sunk quality cost. It delivers measurable return on investment (ROI) by boosting operational performance, enabling growth, and protecting profitability.
The Cost Of Poor Validation: Common Pitfalls And Consequences
Despite being a regulatory requirement, inadequate execution of process validation can lead to significant financial and reputational consequences. Common failures include:
- Failing to establish comprehensive protocols that cover critical parameters.
- Omitting thorough documentation that demonstrates process consistency.
- Neglecting worst-case scenarios in testing process robustness.
- Inadequate risk assessment and mitigation strategies.
Such failures compromise quality and invite regulatory scrutiny. In 2024, the FDA issued 85 Form 483s to medical device firms, compared to just 39 for pharmaceutical companies. This discrepancy may reflect weaker validation maturity in the device sector9.
Figure: FDA Inspection Observations (2006–2024) – Inadequate process validation consistently ranked among the top five citations.9
The financial impact of regulatory action is substantial. According to cGMP Consulting Inc., the cost of receiving an FDA Form 483 can range from thousands to millions of dollars, including remediation, legal fees, and potential recalls. Indirect costs, such as reputation loss and market disruption, can have long-term consequences.10
In short, weak validation jeopardizes compliance, product quality, and financial performance. Robust validation is not merely regulatory insurance — it is a strategic necessity.
Recommendation For Management: Elevate Validation As A Strategic Priority
To stay competitive, organizations must treat process validation as a core business discipline. Key actions for management leadership include:
- Integrate validation into business strategy: Align it with product development and market entry timelines.
- Invest strategically in people and tools: Ensure skilled personnel and robust technologies support validation efforts.
- Promote a quality-first culture: Foster collaboration across quality, manufacturing, engineering, and regulatory functions.
- Leverage data for improvement: Use validation data to monitor trends, drive process optimization, and mitigate risk.
- Proactively manage regulatory exposure: Validate under worst-case conditions and maintain strong documentation.
- Measure and communicate ROI: Use KPIs to quantify validation's impact and reinforce its strategic value.
Final Thought
When management views process validation as a strategic investment rather than overhead, it becomes a driver of competitive advantage. Companies that prioritize robust validation are not just inspection-ready; they are market-ready, resilient, and built for sustainable growth.
References
- Good Practice Guide: Process Validation, ISPE, 2019
- Good Practice Guide -Qualification and Validation, ECA Foundation, rev. 3, 2024
- The importance of COPQ for the pharmaceutical industry; John Johnson, FRSC, CChem, MIQA, NSF Health Sciences 2015
- Apply Cost of Poor Process and Product Quality to Life Sciences Industry, Meyer, K., 2014
- The Real Cost of Poor Quality — And What You Should Do About It, Atkinson S., July 2024
- OEE.com, VORNE Industries, June 2025
- Getting More Value from Logistics Quality, BSI, 2021
- The True Cost of Compliance – A Benchmark Study of Multinational Organizations, Ponemon Institute LLD, 2011
- Datadashboard.fda.gov, FDA, June 2025
- The True Cost of Receiving an FDA 483: A Breakdown of Financial and Operational Risks, cGMP Consulting, 2024
About The Author
Jesper Madsen Wagner is the expertise director for medical devices at NIRAS. He has over 25 years of experience in quality and software compliance for computer systems in the life sciences industry. He specializes in manufacturing, GDP, automation, supplier control, and process validation. With extensive knowledge of global medical device regulations — including ISO 13485, ISO 9001, EU MDR/IVDR, and MDSAP — he has conducted audits worldwide. A recognized speaker at the ECA and a member of the Qualification and Validation expert group, Jesper has held leadership roles in life sciences and consultancy firms. He holds an M.Sc. in chemical engineering from DTU.