Rational approaches to containment implementation for pharmaceutical actives processing: Part 1
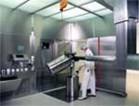
Paper presented at Reed Exhibitions Interphex 2000 Workshop WS-15
March 22, 2000
By Nick Phillips and Terry Fay
Lockwood Greene Engineers
Part one of a three-part article
Table of Contents
Introduction
Personal protective equipment
Facilities requirements
HVAC
Mechanical support
Active powder exposure risks and containment options
Introduction
The trend in today's Pharmaceutical Industry is toward the production of higher potent compounds. These compounds provide more saleable material from each production batch by requiring a lower quantity of active ingredient in each dose. To support this trend, designers are exploring innovations in equipment designs to better contain these higher potency compounds as well as advances in instrumentation to detect smaller quantities of non-contained material. These are being applied to both new production facilities and existing plants, to protect the plant personnel.
Any evaluation of today's pharmaceutical actives requires close attention to Occupational Exposure Limits (OEL) or Exposure Control Limits (ECL). Establishing permissible OEL's is critical to selecting the appropriate technology to achieve the desired containment level. Design Control Limits (DCL), which are the basis of design and testing of systems, are usually set to ½ or less of the OEL.
The basis of containment is to separate the operator from the material being handled. There are a number of ways to accomplish this, and the primary reason for selecting one over another is economic. Therefore, the OEL professional must select a cost-effective solution to provide the required level of containment.
The low operator exposure levels demanded today can be achieved by Personal Protective Equipment (PPE), containing at the source, or by combining the two. In some countries, containment at the source is preferred or even mandatory. For example, in the United Kingdom, the Substances Hazardous to Health regulations enacted in 1988 require that "so far as reasonably practicable, the prevention or adequate control of exposure of employees to a substance hazardous to health shall be secured by measures other than the provision of personal protective equipment."
If establishing permissible exposure limits is critical to proper containment design, how then can containment quantification be achieved? Permissible exposure levels can be determined by analyzing the following considerations:
- Minimum Daily Dose
- Lethal Dose
- Lethal Concentration
- Short Term Exposure Levels
- Occupational Exposure Levels
- Dermatological Absorptivity
Typically these exposure levels are categorized by their potential hazards in airborne concentrations. Containment Categories are determined internally by the company processing the compounds. Examples of typical OEL Categories include:
Category I >100 mg/m3
Category II <100 mg/m3 - >20 mg/m3
Category III <20 mg/m3 - >1 mg/m3
Category IV <1 mg/m3
Having established the control limit, it is possible to select the appropriate technology to achieve the desired containment level. In the case of a cytotoxic compound, containment concepts must be reviewed and criteria established.
The operations, which need to be examined, are any areas in which potent compounds are handled. These typically include, but are not exclusive to:
- Warehouse/Material Handling
- Sampling
- Pharmacy/Central Weigh
- Processing/Formulation
- Packaging
- Mechanical/Maintenance
- Laboratory/R&D/QC
- Waste Disposal
Personal protective equipment
The common belief is that PPE is the lowest cost method of employee protection, since no capital expenditure is involved in equipment purchase or modifications. Unfortunately this does not take into account the capital investment in building modifications and the operating expenses for additional airflow requirements. In addition, protective clothing must be either cleaned or if disposables are used they must be discarded under special conditions, usually incineration and new ones must be purchased. PPE also has a significant negative effect on personnel operating efficiency.
The choice of PPE is based on the mechanism of the active exposure, ingested, inhaled or through dermal absorption. This will determine the type of equipment to be used. At minimum, dust masks should be used (typically limited to category 1 and some category 2 processing). If specific airborne contaminants are identified, such as organic vapors, it is recommended that a negative pressure cartridge respirator be used which includes a solvent rating as well as a HEPA rating. If the active can be absorbed through the skin or has a high toxicity level (typically category 3 and 4processing) a full bunny suit with a Positive Air Pressure Respirator (PAPR) or a clean breathing air supply and mask must be used. Operator beard and mustache must conform to the mask and hood restrictions as defined by OSHA. It should be noted that outer garments are not necessarily impervious to the passage of particles. Woven Dacron/Polyester fibers have grid sizes of up to 50 microns, therefore it is suggested that Tyvek be used which has pores of one-tenth the size. It should also be noted that the Exhausted Clean Room Head Gear (ECRHG) used to avoid product contamination is not necessarily suitable for OEL consideration.
A standard ECRHG has a powered fan creating a negative pressure inside the facemask. This unit draws air from the room through the perimeter of the mask and exhausts it back into the room through a High Efficiency Particulate Air (HEPA) filter. This unit is designed to eliminate product contamination by airborne materials, and does nothing to protect the employee from airborne toxic actives.
A PAPR draws air from the surroundings through a HEPA filter into the operator's mask. The air is then exhausted through the mask perimeter into the surrounding area, protecting the operator not environment. This would be the preferred unit when handling materials, which may create a health hazard. PPE represents only one of the possible scenarios for reducing operator exposure.
Choice of gloves is also important. Double sets of latex or Nitrile gloves are sometimes used but these are easily ripped. A single layer of surgical gloves covered with a heavy overglove is more effective.
Facilities requirements
The ideal facility will focus on personnel and material flow. Their flow should be unidirectional, so that contaminated personnel or containers cannot move into clean areas. Any area where an operator can be exposed to airborne contaminants should be provided with both gowning and de-gowning suites. The gowning room can be an airlock with positive pressure relative to the manufacturing area and the corridor. The operator will enter the airlock from a corridor, put on a full coverall, gloves and PAPR then enter the manufacturing space through a second door. Both doors of the airlock should be interlocked, so that only one can be opened at a time. Materials brought into the room should enter through a separate airlock, which is dedicated for this purpose.
Ideally, when an operation is complete and materials are to leave the manufacturing space, this should be done through an additional material airlock. If space in the area is limited, it is permissible to use one airlock for both inbound and outbound items. The operator will place the items into the airlock and inspect and clean the outside surface if it is necessary.
Once the operator has entered the manufacturing space their outer garment is considered contaminated and must be removed prior to entering the general corridors. To do this they must enter a de-gowning area. Since the operator must remove their outer garment they will be exposed to any contaminants on its surface. This requires that the surface of their garment be treated in some way prior to its removal to reduce the risk of exposure. There are three basic techniques to accomplish this, each require that the personnel enter a room prior to the de-gowning suite. The first is to use a shower, to wash the powders off the surface. This requires either waterproof garments, which are hot and uncomfortable or a complete disrobing of the operator since inner garments may also be wet. The second is a misting booth; the intention is to adhere the material to the surface of the gown so when the operator enters the de-gowning room the particulate will not become airborne. The third is an air shower; these units can be effective if the material to be removed is not sticky or prone to static.
After conditioning the operator enters the de-gowning area. This room is equipped with sinks and if necessary personnel showers. Operators will remove their respirators and clean them in the sinks, then place the cleaned units in pass through lockers to be picked up from the general corridor. Outer garments are carefully removed and placed in a bin for washing or disposal. If necessary the operator will shower. At this point they may leave the de-gowning room into the general corridor.
All the standard concerns of production facilities must also be accommodated, such as safety showers and eye wash stations, sprinklers and fire extinguishers, firewalls and blowout panels, egress stairs and doors and emergency lighting.
HVAC
New and existing HVAC systems can be significantly different from what is normally seen in a GMP facility. Air-Handling Units AHU's, may require upgrading to increase the amount of air changes in the operating area. If solvents are present, it should be a once-through system, with no recirculation (100% outside air). Modifications to a normal GMP system can include:
- Increasing the supply air changes per hour (AC/H) to a minimum of 15 in the process and support areas.
- Providing filters for AHU's with 30% and 95% filtration efficiency.
- Providing terminal supply side HEPA filtration.
- Upgrading the supply fan motor and Motor Control Unit with variable frequency drive and a larger size. This change is not only due to the additional amount of air, but also due to the additional resistance from the HEPA filters.
- Providing exhaust bag-in-bag out HEPA filters with minimum 99.97 % filtration efficiency. HEPA filters should also be installed on dedicated exhausts from shower and supporting rooms. This will keep the exhaust ductwork clean, reduce or eliminate the cost of contracting for cleaning, and eliminate the possibility of cross contamination.
- Upgrading the exhaust fan motors, along with the variable frequency drive, with a larger size due to the additional resistance from the exhaust bag- in bag-out HEPA filters.
- Providing stainless steel ductwork for supply and exhaust distribution system to reduce the possibility of leakage and to aid in cleaning.
- Providing a control and monitoring DDC system dedicated exclusively to the contained operations areas. The system should have pressure differential, temperature, and humidity sensors and controllers for each room, maintaining airflow according to required direction and pressure. The system should have a dedicated panel, which is connected to the central monitoring and control, it will also include necessary alarms within the operating areas. Status panels are mounted in each of the operating and mechanical areas. Operating status of AHU's are displayed and can be viewed on these monitoring panels.
Mechanical support
All fumes and vapors from charging process equipment such as: reactors and dryers should be contained by laminar flow units or glove boxes. This will eliminate the need for utilizing flexible trunks when manways or charge ports are open. The use of flexible trunks should be avoided since cleaning them is difficult and operators can be careless with their positioning. All process area fumes collected by the exhausts should be sent to a scrubber or Thermal Oxidizer. Flexible trunks may be utilized when handling drums of solvents (containing no actives) for additions and transfers.
Active powder exposure risks and containment options
General
The primary areas of exposure to airborne powders take place during material transfers and "makes and breaks," that is the time, wherein a container is coupled or de-coupled from a reactor, mill, mixer, dryer etc. Powdered actives are contained by several approaches:
- Limited access areas
- Controlled airflow designs with controlled pressures and filtration
- Process modifications to eliminate high exposure procedures
- Totally self contained processing
- Automation
- Personnel Protective Equipment (usually for maintenance, upsets and HAZOP situations)
For Category 1 processing, simple limited access rooms with controlled general directional airflow schemes are implemented. For Category 2 operations (and where dermatological exposure is not a problem), local exhaust systems and directional airflow (laminar flow booths) can be used. These systems are typically considered to be effective down to levels of 50 to 100 µg/m3. With the addition of ergonomic controls and specific SOP's companies like Extract Technology have designed systems of this type capable of levels less than 10 µg/m3. This would include Category 3 materials for some special applications.
Category 3 and 4 compounds are typically handled in several ways. With new products, high exposure operations are being designed out during product development, for example, tray dryers and open filters are being replaced with contained filter dryers. These units themselves are also being improved for better containment of feed, discharge, and sampling, and should be equipped with Clean In Place (CIP) capability.
The transfer of these materials to and from totally contained processes in reactors, filter dryers, and fluid bed granulators must take place using specialized couplings which limit the amount of material escaping into the general processing area. The containment requirements for sampling, charging and discharging, and cleaning may indicate the use of glove boxes or as in the case of handling radioisotopes fully automated robotic systems.
As in any properly designed GMP facility, all raw & packaging materials required for batches should be brought into the operation as needed through the material/equipment airlocks. Materials should be delivered to the airlock from a clean corridor. The corridor side door and process side door should be electronically interlocked so that only one door can be opened at any time. Once the material has been delivered into the airlock the operator in the process area will open the process side door and bring the items in.
Receiving
All active ingredients requiring containment should always be received in small quantity, hard sided containers. This will reduce the chance of a catastrophic failure. Any containers with leakage should be handled as a HAZOP situation.
End of Part 1. Click here to read Part 2.
For more information: Nick Phillips (nphillips@lg.com) or Terry Fay (tfay@lg.com), Lockwood Greene, The Tower, 270 Davidson Ave., Somerset, NJ 08873-4140. Tel: 732-560-5700.