Recent Developments Identifying Interactive Factors Affecting Tablet Scuffing Seen In The Aqueous Film Coating Process
By Fred A. Rowley, Solid Dosage Training
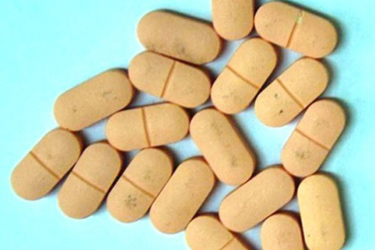
In 2013, I published preliminary findings concerning the scuffing phenomenon often seen during aqueous film coating.1 These findings came from observations of small- to large-scale manufacturing in seven coating departments of six different companies and identified the use of titanium dioxide as a factor. Since that time very little research has been published advancing our understanding of this fleeting tablet defect.
In general, the literature falls short of defining the exact causes of the scuffing phenomenon, appearing almost as suggestions and often to the point of simply guessing rather than providing science-based answers. Further, as with other defects seen in both tablet compression and aqueous film coating, there is usually more than one root cause.
In the absence of dependable guidance, many firms, having neither the time/resources nor the interest, simply apply the “poor man’s answer” to this problem and coat the pan with the same coating suspension before the formal coating cycle begins. And this of course prompts the questions of whether the practice is documented as part of the permanent coating record and if specific instructions are incorporated into the master batch record. In addition, it should be noted that this suspension may dry and flake during an extended coating process and be deposited on random tablets. Hence, in reality, you fix one problem but introduce another. Examples are seen in Photos 1 and 2.
Photos 1 and 2: Examples of coating flakes.
Over time, companies accepted that “this is just part of the process” and, with no other established remedy available, allowed the practice.
In a separate development, we now have movement in the European Union to remove titanium dioxide from food products, including coating formulas for tablets.2Until this change becomes law, in the interim, it might be easier to revisit the problem and determine how to either reduce or eliminate the defect. Why not first review the state of your manufacturing process?
We begin by asking two simple questions:
- Why do formulas with a small quantity of titanium dioxide almost never exhibit scuffing, even with large pan charges?
- Why do mixing systems with a recirculation loop, coupled with a basic homogenizer, almost never produce scuffed tablets, even with formulas containing a large quantity of titanium dioxide?
Today, current knowledge has proved that scuffing is actually an interaction of up to three separate factors. It is also important to recognize that all three factors may be stand-alone root causes or an interaction, depending upon an individual situation or general condition.
Confounding perfect understanding, in large-scale manufacturing, scuffing may occur at any time throughout the coating run but is most often observed during the last portion of the coating cycle. For example, when using a 48-inch (120 cm) coating pan with a 70-minute theoretical coating cycle to achieve a specification of a 2% w/w film build, we would frequently see scuffing appear during the last 15 minutes. There are some observations that find scuffing appears earlier in the coating cycle, but they are quickly covered by subsequent coating and may not be seen at process end.
The fact that this defect appears late in the coating process may be linked to the suspension mixing and holding process and to a particular formula.
Root Cause #1: Formula
As seen in Table 1 below, a typical coating formula is made up of both water-soluble and water-insoluble components. Iron oxide and titanium oxide are not water-soluble, hence the proper term suspension is applied once the formula is mixed into the water vehicle. Recognizing that most coating formulas are suspensions and therefore must be both mixed and held properly is the first part of the complete answer to the scuffing problem. Reviewing your current batch record may reveal that the suspension holding process is not even mentioned.
Table 1: A typical aqueous film coating formula
And if you are in pharmaceutical or generic manufacturing you usually face an additional problem: changing the formula costs time and money. Knowing this, the “poor man’s answer” becomes more attractive.
In some cases, where titanium dioxide is the primary component of a white color formula, it may not be possible to avoid some scuffing due to the preponderance of the material. In this case, frequent passivation and constant stirring or recirculation of the coating suspension becomes even more critical to minimize the frequency of tablet scuffing.
Root Cause #2: Mixing And Holding Practices
Many master batch records reflect mixing and holding practices recommended by preformulated raw material suppliers for small or R&D batch sizes. Considering the highly variable quantity of titanium dioxide that may be present in any formula, a specific mixing time for all concentrations and for any quantity of suspension to be coated cannot be correct in all situations.
For example, consider the quantity of suspension required for a 60-inch coating pan holding 350 kg tablets and you can better understand potential mixing and holding issues that were never observed in R&D. This is in fact a very real issue for large-scale manufacturing. Photos 3 and 4 demonstrate this point. Holding a mixed suspension over a period of hours becomes a critical operating parameter and is key in reducing tablet scuffing.
Photos 3 and 4: Examples of R&D and commercial mixing tanks
The same type of equipment and mixing process successfully used at the small scale, coupled with inadequate holding practices at the large scale, may combine to produce a bimodal distribution of titanium dioxide. And this can be greatly amplified with formulas containing a large quantity of titanium dioxide.
This process deficiency is readily confirmed by auditing the hold tank and the various solution lines at the end of any coating cycle. If a small quantity of a white viscous suspension is sometimes seen during post process inspection or during cleaning, it is evidence of perfect mixing but deficient holding. This is especially valid with a white coating containing a high quantity of titanium dioxide as it is impossible to visually distinguish a well-mixed and maintained suspension from a bimodal mixture.
In reaction to these observations, using a homogenizer combined with a recirculation system has proved to reduce or eliminate this problem. As a result, formulas containing high quantities of titanium dioxide are both mixed and maintained successfully.
Photo 5: An example of a homogenizer.
Root Cause #3: Coating Pan Passivation Practices
Passivation practices widely differ between companies and sites. It is important to understand that after initial equipment installation and qualification, at which time passivation is usually performed, subsequent pan passivation can vary based more on maintenance department policy than on production need. And the need may change greatly depending upon the type and frequency of formulas coated in any single coating pan. Therefore, the practice must be a reaction to content and production frequency. Combine formulas with large iron oxide content with infrequent passivation and the result may be excessive iron oxide residual caught on the pan surface. This accumulation is not easily dislodged.
It is in fact frequently dislodged by titanium-rich “slugs” randomly deposited on tumbling tablets. The interaction supports copious physical evidence where the tablet that receives the titanium slug is not necessarily the tablet that exhibits the scuff of iron oxide.
This observation is confirmed with a second observation that the quantity of scuffed tablets can change between different pans from the same batch of tablets and from different batches in a single coating campaign. These random slugs are deposited at the bottom of the mixing tank or in the coating transfer lines during inadequate mixing and more often during inadequate holding over extended coating cycles. The greater the quantity of slugs, the greater the quantity of scuffed tablets.3,4
Further, titanium slugs have been linked with the tearing and peeling of the coating from tablets sliding against the coating pan regardless of the pan capacity used.5 It is, however, important to note that this particular problem is more often observed with small batch sizes in larger pans rather than with larger pans at full capacity.
Photo 6: We see small slugs that have been isolated after mixing a red color solution using a #80 mesh screen.
Conclusion
There are three primary root causes of tablet scuffing. Minimizing or eliminating titanium dioxide reduces or eliminates scuffing.
Appropriate tank sizing, suspension mixing, and suspension holding practices are key and sometimes mandatory for a high-quality product. Assuming that an appropriately sized tank with any type of suspension mixing while ignoring the importance of suspension holding practices is dangerous.
Passivation should be a reaction to process requirements, with frequent passivation mandatory in some cases.
Recommendations
- Companies should review all coating formulas with a goal to identify those containing titanium dioxide as a major component.
- Review and, where appropriate, alter your mixing and holding practices.
- Passivate the coating pan based on manufacturing needs, not on established maintenance schedules.
References
- Rowley, F : “Toward a Greater Understanding of The Scuffing Phenomena Observed in Aqueous Film Coating”, Tablets and Capsules Magazine, 10 (3), 2012.
- Biogrund company bulletin: “Film Coating: Replacement of titanium dioxide (TiO2) in tablet film coatings”, undated.
- Y. Ogasawara, R. Steffenino, C. Cunningham, Scuffing Measurement Methodology and Improved Film Coating Systems, American Association of Pharmaceutical Scientists Poster Reprint. (2008)
- Rowley, F, A: “Tablet Scuffing Lecture, Indian Pharmaceutical Congress, Guest Lecture, 2023.
- BASF company bulletin: “Film Coating Scuffing”, 2014.
About The Author:
Fred A. Rowley has more than 40 years’ experience in the pharmaceutical and nutritional supplement industries in manufacturing, technical services, and R&D settings, with particular expertise in solid dosage manufacturing and training. He has knowledge of the granulating, blending, tablet compressing, and film coating processes for more than 800 API drug substances. He is and has been retained as a subject expert by law firms, equipment manufacturers, international pharmaceutical and nutritional supplement companies, and compounding pharmacies, and has lectured at the FDA, the ISPE, and at many colleges of pharmacy around the world. Previously, he has been director, manufacturing technical support, for Watson Laboratories; plant manager, tablets and capsules, Weider Nutrition International; vice president, operations, Arnet Pharmaceuticals; OROS operations manager, Alza Corporation; and bulk solids manager, Syntex FP, Puerto Rico.