Retrofitting Facilities For Modern Bioprocessing And Pharma Production
By Kyle Winn, head of production, North East and North Cumbria Medicines Manufacturing Centre
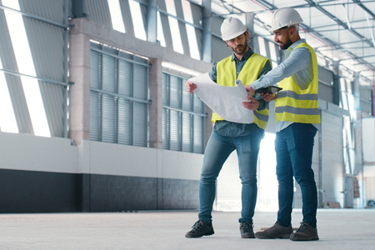
The pharmaceutical manufacturing landscape is evolving rapidly, with increasing demand for monoclonal antibodies (mAbs) and advanced therapy medicinal products (ATMPs). These highly specialized therapies require stringent facility design considerations, particularly when retrofitting existing structures or designing multi-product facilities.
The Medicines Manufacturing Centre (MMC) is a £30 million ($38 million) multi-modality aseptic manufacturing project underway in the U.K. by the National Health Service. The facility will focus on the production of small molecules, mAbs, and antibiotics, converting an existing warehouse into a state-of-the-art ready-to-administer (RtA) manufacturing site. Set to commence operations in 2026, the project has already provided valuable lessons for those looking to repurpose older facilities for advanced pharmaceutical manufacturing.
Advantages And Challenges Of Retrofitting Old Buildings
Retrofitting offers several advantages, making it an attractive option for pharmaceutical manufacturing. One of the key benefits is cost efficiency. By utilizing an existing structure, organizations can significantly reduce initial capital expenditure compared to new builds. Additionally, retrofitting can expedite project timelines, as planning permissions and infrastructure are often already in place, enabling a faster transition from design to operational readiness.
Another major advantage of retrofitting is sustainability. Reusing existing structures minimizes the environmental effects by reducing the need for raw materials, demolition waste, and carbon-intensive construction processes. This approach aligns with global sustainability goals and corporate environmental responsibilities.
However, adapting older facilities for modern bioprocessing and pharmaceutical manufacturing comes with inherent challenges. One of the first considerations is whether to retain only the shell or preserve additional infrastructure. This decision demands a comprehensive evaluation of the existing mechanical, electrical, and plumbing systems to determine compatibility with GMP requirements and building regulations. Given the 2022 update of Annex 1, this has become even more critical, as key infrastructure like air handling units (AHUs) and ductwork from a legacy facility are unlikely to be suitable for the updated guidelines.
Structural integrity is another major concern when repurposing older buildings. The facility must be assessed to ensure it can support the weight and vibration sensitivity of modern bioprocessing equipment. Upgrading utilities is often necessary, as older power supplies, HVAC, and water systems may not meet the stringent demands of pharmaceutical manufacturing. At MMC, we faced this challenge head-on, ensuring that our facility could support high-grade cleanrooms and equipment without compromising efficiency or regulatory compliance by essentially using a warehouse shell and constructing a brand-new facility within.
Factors such as humidity control for vaporized hydrogen peroxide (VHP) cycles, containment for genetically modified organisms (GMOs), and stringent temperature regulations must be carefully managed in both new and existing facilities. Controlling humidity is critical to ensuring effective VHP decontamination, while strict temperature controls are essential for maintaining product stability and quality. Additionally, robust containment measures must be designed to meet biosafety requirements, particularly when handling advanced therapy medicinal products (ATMPs) or other high-risk biological materials.
Advantages Of A New-Build Facility
When considering whether to retrofit or build from the ground-up, it’s important to consider the advantages and drawbacks of both approaches. One of the most notable benefits is the ability to design the facility exactly as required with minimal compromises or workarounds. Starting from scratch allows for the implementation of optimized workflows, ensuring that the facility is tailored to meet GMP requirements efficiently. While designing a new facility may add time and cost to a project — particularly if additional planning is needed for external structures — it eliminates the risk of uncovering unforeseen issues that often arise in retrofitted buildings, such as hidden structural elements or space constraints.
Another key consideration in new builds is site ownership. If the facility is built on land that is owned outright, there is full control over design, maintenance, and modifications. However, if the site is leased, a strict landlord agreement is essential, particularly for maintenance responsibilities. Additionally, integration with the wider site infrastructure, such as CCTV access, fire alarms, and general security systems, must be considered.
Beyond internal logistics, a new facility’s effects on the surrounding area must not be overlooked. While new pharmaceutical manufacturing sites can bring significant economic benefits to local communities, there are potential challenges related to transport links and amenities. Effective engagement with local authorities and the community is crucial for long-term success, ensuring that the facility is seen as a positive addition rather than a burden.
Service requirements are also a critical factor when developing a new pharmaceutical manufacturing site. Availability of essential utilities, such as electricity and water quality, can significantly affect facility operations. If purified water systems are required, the local water supply must meet stringent specifications to ensure compliance with pharmaceutical-grade requirements. Similarly, air quality is a key consideration, particularly if the facility is near busy roads or coastal areas where contaminants like particulate matter and salt can affect AHU performance. These factors must be thoroughly assessed in the planning phase to prevent long-term operational challenges.
Disadvantages Of A New-Build Facility
Despite the benefits, new-build facilities come with several drawbacks. The most prominent challenge is cost. Constructing a facility from the ground up requires substantial capital investment, and unforeseen expenses can arise during the design and construction phases. Additionally, regulatory approvals and planning permissions can be time-consuming, delaying project completion and increasing costs.
Another disadvantage is the extended timeline associated with new builds. Unlike retrofitting, which can leverage existing infrastructure, new facilities require significant lead time for design, approvals, and construction. This delay can impact the speed at which an organization can respond to emerging industry demands, particularly in rapidly evolving fields like ATMPs.
Finally, environmental impact is a concern when constructing a new pharmaceutical facility. The carbon footprint of new builds is considerably higher than retrofitting, as construction processes generate substantial emissions. Sustainable design choices, such as energy-efficient HVAC systems, solar panels, and waste reduction strategies, can mitigate some of this impact, but the initial environmental cost remains a consideration.
Overcoming Historical Contamination And Cleanability Concerns
One of the most significant concerns when working with an existing building is its prior use. Legacy contamination from past manufacturing activities must be carefully evaluated. The risk of unseen residues embedded in walls, ceilings, or ductwork poses a challenge to maintaining cleanroom-grade standards. Addressing this requires a thorough decontamination strategy, alongside the installation of non-porous, GMP-compliant materials that can withstand rigorous cleaning protocols.
Cleanability also extends to architectural elements such as flooring and drainage. In a pharmaceutical setting, floors must be seamless and impervious, preventing microbial retention. The same applies to walls and ceilings, where the choice of materials plays a vital role in reducing the risk of contamination. At MMC, we implemented a design that ensures ease of maintenance, minimizing potential contamination risks in the long run.
Site Coordination And Infrastructure Challenges
Retrofitting a pharmaceutical manufacturing facility requires meticulous coordination across multiple contractors. At MMC, we navigate a highly complex environment where four to five contractors are working on different projects simultaneously. It is important to note that these contractors are not directly part of our project; they are involved in other site developments, such as constructing the new welfare area, which includes a gym and restaurant for staff, or bringing in additional power supplies via high-voltage cables and additional substations. Managing multiple projects simultaneously requires robust coordination and project management to ensure alignment and minimize disruption.
Choosing the right site location is equally crucial. Initially, MMC was planned for a different area within the facility, but we identified potential conflicts with HVAC inlet locations from other site operations. This led to a strategic relocation, allowing us to optimize airflow management, materials flow, and contamination control.
Designing For Containment And GMP Compliance
MMC will use a mix of pressure bubbles and pressure sinks to maintain strict environmental control between cleanroom areas. These systems create containment zones by directing airflow to prevent cross-contamination in the event of spillages. Pressure bubbles maintain higher pressure to push air into lower-pressure sinks, ensuring contaminants are kept away from critical areas. Pressure sinks, in turn, help contain and safely manage any potential contaminants by drawing air away from sensitive zones.
The design process and documentation control are critical in any build, whether retrofitting an existing facility or constructing a new one. Pharmaceutical facilitiy design in the U.K. must be comprehensive and reach a level of detail at which every aspect of the facility — including socket placements, ventilation, extraction, data points, and drainage — is fully mapped out.
To ensure GMP compliance, the design process follows a structured approach: validation master plan, user requirement specifications, design qualification, installation qualification, operational qualification, and performance qualification. Any deviations from the design, user requirement specifications, or validation master plan must be documented within the deviation or change control procedure for GMP aspects, while HTM-related deviations should be recorded within the derogation schedules and assessed by the relevant authorized engineer for healthcare facilities.
Our facility also incorporates isolators and closed manufacturing systems to minimize operator intervention, improving sterility assurance. The isolators will be VHP-positive pressure, externally ducted, unidirectional air isolators. These isolator designs are critical in reducing contamination risks by ensuring that operators have minimal direct contact with the aseptic process. They are equipped with integrated monitoring systems, automated decontamination processes, and ergonomic features that enhance operator efficiency while maintaining GMP compliance. Additionally, access control systems ensure personnel cannot enter production areas without completing appropriate changing and gowning procedures, reinforcing GMP compliance at every stage.
MMC’s Role In Shaping The Future Of Pharmaceutical Manufacturing
The MMC represents a vision for the future of pharmaceutical manufacturing in the U.K. Designed with adaptability at its core, MMC is equipped to support evolving production needs, ranging from monoclonal antibodies to small molecules.
Beyond compliance, MMC is focused on fostering innovation. We integrate advanced technologies such as digital twins, computational fluid dynamics, automation, and data analytics to enable continuous improvement and process optimization. Our role as an integral part of the NHS ensures that our initiatives align with regional and national healthcare priorities. This includes monitoring drug shortages, supporting the development of new treatments, and contributing to national standardization initiatives for ready-to-administer products.
About The Author:
Kyle Winn serves as the head of production within the North East and North Cumbria Medicines Manufacturing Centre. He is the professional lead for England for the Association of Pharmacy Technicians, and is the director of an aseptic production consultancy, WinnPharma.