Selecting Secondary Packaging For Bio/Pharma Products — What You Need To Know
By Carla Reed, president, New Creed LLC
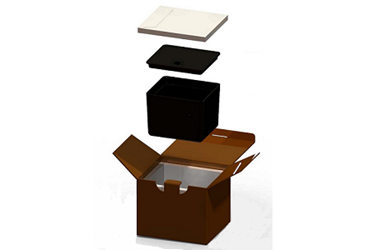
Once a small or large molecule product has passed the various hurdles in clinical trials, it faces important considerations related to market acceptance and commercialization. Irrespective of the nature or formulation of the product, there is always a heavy focus on the primary packaging element — the final unit of use. In most large companies (and probably many smaller ones) there is a team of experts engaged in designing packaging, taking into account geographic preferences, regulatory requirements, and patient profiles.
A great amount of time and money is spent on evaluating dispensing units for sprays and inhalants, blister-packs versus bottles for individual dosage of tablets and gel-caps; the list is extensive. Then there is the literature, labeling, and even the folding of package inserts (and their location within the package), all of which must be reviewed by teams of experts. Considerations include the protection of the product, ease of use at the time the product is consumed, ergonomics, and other issues for nurses, patients, and other parties. These are critical issues that a whole industry is involved in evaluating and perfecting.
As a supply chain person, I am always thinking about things like packaging from a different perspective. Considerations that are important to me — and should be to others in the business of moving things around the world — are how well the packaging component fulfills its function of product protection in variable situations.
A recent conversation with a colleague, in which he compared the package experience to that of a passenger experience on a transportation device, put my mind on an interesting train of thought. Unlike a passenger who has the ability to respond to changes in the environmental conditions during a journey, the inert package is pretty much at the mercy of the resources engaged in transporting it from origin to destination. Unable to express displeasure or alarm at unexpected events, packages are left in harmful conditions – at receiving and shipping docks, on airport tarmacs — or even worse, left behind.
The solution — providing packages with the ability to respond to unplanned events and conditions, raising the alert as needed — is a viable reality.
There are many options available for improving the package experience by using protective packaging, including active and passive temperature monitoring and control, as well as sensors that communicate in near real time. The ongoing location and state of the material, as well as its point in the chain of custody, can be monitored through an increasing number of wired and wireless information systems and alerting technologies.
Secondary packaging, at times an overlooked element of product life cycle management, should provide protection for the material or product across all the process steps, from final packaging at production through consumption, return, and disposal. Understanding the process flow, activities, participants, and risk factors across an increasingly extended chain of custody is the first step. Environmental conditions, with risks of variations in temperature, humidity, and altitude, tend to get the most attention. Other factors include light sensitivity, orientation, air pressure, shock, and vibration — any of which can have a negative impact on fragile biological materials, even when they are cryopreserved.
Considerations For Packaging
During the product development process, different physical, chemical, and biological characteristics are recorded, along with their related stability profiles. Stability data and related impact of different environmental conditions contribute to the product profile and registration documentation that is filed with appropriate agencies. These are based on relatively predictable environments, encountered in controlled situations. When evaluating packaging requirements for distribution, this baseline should be expanded upon, taking into account a broad spectrum of potential variables that may be encountered as materials and products are handled, stored, and transported across an extended supply chain environment.
To address environmental conditions and temperature variations, packaging components are designed to incorporate insulation (polystyrene, polyurethane) and preconditioned gel packs, phase-change materials, and dry ice. Other concerns include vibration, orientation, shock, and other hazards, which are addressed with additional packaging components. The result is large boxes, pallets, and other bulky tertiary packaging that creates other challenges that need to be considered. For example:
Material Handling Capabilities
In addition to the impact of environmental variations, it is important to take into consideration the handover points in the chain of custody, each of which may have different levels of capability for material handling and control. For example, a warehouse or interim storage location will have appropriate equipment to handle large, bulky, and heavy items. This is not so for interim trans-shipment points in air transportation, especially for smaller aircraft, where transfer may take place at plane side. And in the case of clinical samples or products that are being shipped into a hospital or clinic, material handling limitations are an even greater challenge.
Point of Use Requirements
Another consideration, and not one to be overlooked, is the level of protection you need to provide for the product after it has been delivered.
Manufacturing Environment
There is increasing use of customized disposable components for use in the processing of biological products. These include a variety of components, many of which are installed in a sterile environment (for example, filling needles for vials and ampules). In many cases, these installations take place in an isolator, with restricted movement for operators who are unpacking sterile components from their enclosures. Packaging design needs to consider the impact of transportation hazards on all elements, as well as the restrictions protective packaging may have at the point of use.
Clinical Environment
Bulky packaging that provides the correct level of protection during transportation is not suitable for storage and handling of products in a clinical environment. Ensuring that each of the steps in the process, post receipt, have been evaluated for risk factors for material handling is critical. For example, removing a cryopreserved product, with extreme friability, from the protective transportation packaging is no easy task. Risks include bumping, dropping, or other activities that could fracture the material, compromising the efficacy and endangering the lives of patients.
Understanding the material handling limitations and constraints and building mitigation approaches into the packaging strategy are imperative. Providing appropriate instructions and training guides is another activity that should not be neglected -- or taken for granted.
Smart Packaging: Integrating Sensors To Raise The Alarm
Current practice for time- and temperature-sensitive materials and products is to place data loggers in the packaging to track deviations from desired temperature range and record excursions. In many cases these are passive devices — data captured is downloaded and evaluated once the item has reached the destination and been unpacked. At that point, the damage has already been done and the material is lost.
A better practice is to include active data logging devices in the packaging component — potentially using a combination of devices to log temperature, shock, vibration, or any of the hazards that could impact the efficacy of the material. These devices, coupled with GPS capabilities and information systems to reflect the data that is being captured, provide a near real-time record of both the location and state of the item. At times termed “rescue packaging,” the inclusion of sensors and monitoring devices provides the inert package with the ability to raise the alarm. Access to information related to deviation, location, and entity within the chain of custody facilitates intervention. It is a proactive, rather than reactive, response that can make all the difference.
Risk Assessments/Reviews
One of the guiding principles when manufacturing and distributing life sciences materials and products is to integrate FMEA (failure modes and effects analysis) into each of the process steps. Risk assessments to identify hazards and impact should be performed for all materials and products. And these are not restricted to finished products. Raw materials, reagents, APIs, and other starting materials should be included across the product life cycle.
Material handling constraints and risks at the points of packaging, transportation, interim storage, receipt, and unpacking should be documented and evaluated in a structured risk assessment. Following a “what if” approach, coupled with an understanding of each of the process steps and constituents, will provide the baseline for developing the packaging strategy. The subject of transportation planning for time- and temperature-sensitive materials has been covered in a previous article. But these are not the only considerations when selecting secondary packaging components.
Selecting The Right Packaging Based On Product And Shipment Profiles
When selecting packaging for high-value, fragile, and generally vulnerable materials, it is common to err on the side of caution. The result, bulky packaging with many components to pack and unpack, not only increases the cost of transportation, but creates disposal issues at the point of receipt. There are many options that are more economical in terms of space and level of effort to pack. Packaging companies have introduced many innovative designs and materials, most of which come in reusable configurations. Replacements for traditional (and environmentally unfriendly) expanded polystyrene (EPS) include options that provide better insulation while having a smaller format. Two examples include:
- Polyurethane (PUR) that can be molded into different shapes and thickness. This provides greater insulation than equivalent thickness of EPS. In addition, with a smaller form factor, the volume-to-weight ratio results in reduced transportation costs (particularly for air transportation, where volumetric weight is a factor).
- Vacuum insulated panels (VIPs) are airtight enclosures that provide better insulation than either EPS or PUR. This is a more expensive option but is an excellent choice for reusable packaging, customizable for specific applications.
These are not the only choices; other options include active packaging components with integrated sensors or GPS tracking and mechanical or electrical assistance to ensure temperature control.
Last, But Not Least: Labels
Finally, packaging is not complete without the correct labels and related documentation. When conducting the risk assessment, it is important to take into consideration each of the handover points in the shipment life cycle and chain of custody. Labels and documentation should support different levels of literacy and language. Clear labeling for material-handling hazards (orientation, shock, temperature, vibration, etc.) should provide indicators to ensure the desired level of care.
Conclusion
Secondary (and tertiary) packaging is an important element to ensure that the time and investment spent in developing life sciences products are not wasted. Taking the time and effort to evaluate the risks and develop remediation activities is important.
And if in doubt, call in an expert. Providers of packaging products — and related technology components — have the expertise and experience to assist.
About The Author:
Carla Reed is a seasoned supply chain professional with more than 25 years of experience providing leadership and program management across a variety of programs for the life sciences industry. Her broad range of experience and expertise has provided solutions for pharmaceutical and biotech companies challenged by the growing complexity of extended supply chain environments. Her firm, New Creed LLC, provides change leadership to facilitate sustainable solutions, providing hands-on experience in all aspects of supply chain operations. You can email her at carla@newcreed.com or connect with her on LinkedIn.