Speed Up Your AAV Vector Development And Manufacturing With A HEK293 Suspension-Based Platform
By Niklas Krämer, Anica Schmidt, Sandra Klausing, Gina Cheung, Alyssa Vetter, Kathrin Teschner, Catherine Buchere, Carole Langlois, and Sandrine Chevalier
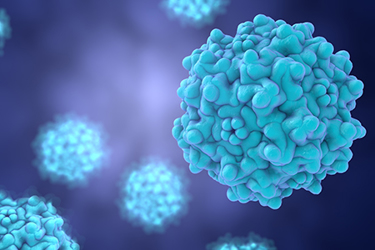
Adeno-associated viral vectors (AAVs) are among the most widely utilized vectors in gene therapy applications due to their efficiency and versatility. Traditionally, large-scale adherent production of viral vectors like AAV has relied on various cultivation systems, including roller bottles, CellSTACKs (Corning), CellFactories (Nunc, ThermoFisher Scientific), fixed bed reactors, and microcarrier-based cell culture. These methods have been extensively employed to meet the demands of gene therapy production. However, there are compelling reasons to consider adapting your process to suspension culture.
Suspension culture also offers greater flexibility regarding scale and volumes per process. This flexibility is crucial for adapting to varying production needs and optimizing resource utilization. Improved scalability is another benefit, as suspension culture can lower operational costs compared to running multiple parallel processes. This cost efficiency is particularly advantageous for large-scale production. Furthermore, using controlled cultivation systems in suspension culture enhances optimization potential. These systems allow for precise control over cultivation conditions, which leads to better consistency and quality of the viral vectors produced.
Explore how adapting to suspension culture for AAV production can offer significant advantages in terms of serum elimination, flexibility, scalability, optimization potential, and regulatory compliance.
Get unlimited access to:
Enter your credentials below to log in. Not yet a member of Pharmaceutical Online? Subscribe today.