The 3 Big Barriers To AMT Implementation

By Katie Anderson, Chief Editor, Pharmaceutical Online
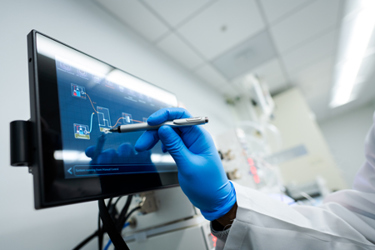
Advanced manufacturing technologies (AMTs) can not only lower costs but also improve the quality and consistency of both API and final dosage manufacturing in pharmaceuticals, so why are they not more widely implemented? According to Dennis Hall, vice president of Advanced Manufacturing Technologies for US Pharmacopeia, manufacturers are hesitant about cost, regulation challenges and the staff needed to implement such technology.
Long-Term Cost Analysis
It takes a great deal of money to invest in a new technology, and generic drug manufacturers have tight profit margins. In addition to that, the manufacturers may see no need to add technology when they have fully functional machinery at their site with no current issues.
Shifting this cost-conscious and problem-driven mindset will prove difficult, especially during an unsure economic time. But, Hall adds that investment now can lead to more ROI down the road. This can be addressed with a full assessment of investment and long-term planning. “We need to help companies think through not just the next two years, but perhaps the next 10. Yes, there's money to invest now, and here's where your savings is in years four, five, and six,” added Hall. Take time to look at the long-term cost/benefit analysis rather than getting caught up in short-term thinking is Hall’s biggest piece of advice.
Regulatory Barriers
There is also some hesitation regarding perceived regulatory barriers. Hall notes that this is “perceived” because the FDA will say that there isn’t a regulatory barrier. “Companies have been doing it a certain way for 20 years, and they know what questions the FDA are going to ask. If they do it a different way, they don't know what questions the FDA are going to ask, so they may avoid that risk,” noted Hall.
To reduce this regulatory fear, Hall’s team at USP is working on standardizing the questions that the FDA will ask for new AMTs to set a guideline for manufacturers. They are looking to establish new technology QA language for both the manufacturer and the FDA to better navigate the regulatory road ahead.
Hall advised not to be afraid to talk to the FDA about questions and issues. “They're willing to engage early. I've seen too many examples of folks saying I don't want to engage FDA until we figured this out, whereas engaging with them early can help you figure it out,” he furthered.
Workforce Training
There is also a barrier surrounding training and the workforce, according to Hall, with new technologies often requiring a different skillset to run. “We need to support the development of new curricula in colleges, work training programs, etc., to be able to have a skilled workforce that can actually use these new technologies,” he added.
USP is involved with an organization called the Alliance for Building Better Medicine, where they regularly talk about the inability to find talent to run the new lines that are being built down through that program.
Moving The AMT Needle Forward
Hall wants to emphasize that the adoption of AMTs is more about solving industry problems than adopting a new technology because it is shiny and new. “It's not as much we want to help people implement continuous direct compression, it's around what problem that the industry needs to solve and seeing what technology helps them solve that problem,” he furthered.
The USP’s Advanced Manufacturing Technology team established a lab in recent months in Rockville, Maryland that is dedicated to just that. The team there is not only focused on developing and scaling new AMTs, but it is also set up to help manufacturers with their own problems and issues. “We can solve issues from a testing perspective or a manufacturing decision. We have a lot of capabilities that the industry may not think of from USP,” added Hall.
In addition to the AMT Lab, USP is also working on a host of other projects to help the industry move forward. Its Medicine Supply Map helps provide the full picture of supply chain, so manufacturers can prevent disruptions. Later in 2025, it will also unveil its exciting Key Starting Material Module.