The Business Value Of Connectivity For Product Inspection Equipment
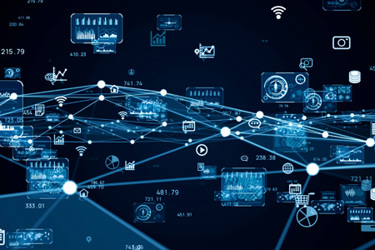
Connectivity is the ability to communicate through a network. It allows data exchange between hosts. A host is any system that executes software applications, including computers, mobile devices, and PLCs (Programmable Logic Controllers). Automated machines, such as product inspection equipment, are controlled by applications executed on a host inside the machine. These applications use data for three main purposes:
- Automation of tasks performed by the equipment
- Communication with personnel, for example, by displaying information on a screen
- Communication with connected systems in a network
Applications executed on separate hosts can only communicate if their hosts are connected to the same network. Additionally, both hosts must execute the same communication protocols (software rules that manage data exchange). The result of data exchange is an identical copy of application data on both hosts. This ensures both applications have the same information.
Product inspection equipment is particularly rich in valuable data, because it continuously evaluates the production process. Product inspection data is used by a variety of systems and personnel. And connectivity is the most efficient method to distribute data to many users. This paper is a business guide to connectivity for product inspection equipment. It is intended to help business personnel convey their needs to engineering, contractors, and IT departments (Information Technology). This paper avoids many of the complexities of communications technology. Instead, it focuses on the value of connectivity, and more specifically, the value of information provided by checkweighing, metal detection, vision inspection, and x-ray inspection.
Get unlimited access to:
Enter your credentials below to log in. Not yet a member of Pharmaceutical Online? Subscribe today.