The Future Of Cell And Gene Therapy Storage And Transportation
By Vince Paolizzi, Director of NanoCool Sales, Peli BioThermal
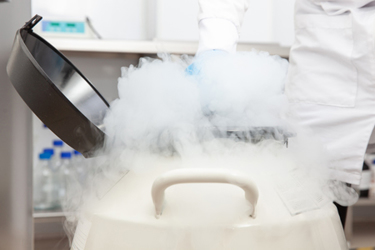
Vaporized liquid nitrogen is currently the only workable means of maintaining the ultra-cold temperatures necessary for certain therapeutics and tissue samples. While dry ice is a feasible solution for keeping packages between -20 and -80 C°, colder applications often necessitate the use of liquid nitrogen. This paradigm has resulted in a number of logistical challenges for biopharmaceutical companies, clinical trial sponsors, and healthcare providers, as both the temperature requirements for COVID-19 vaccines and the increasing proliferation of temperature-sensitive biotherapeutics has made ultra-cold storage capacity more critical than ever.
Many companies have worked overtime to expand their ultra-cold chain operations, resulting in new challenges for their shipping operations, both in terms of scale and handling. These challenges extend to home collection shipping, particularly direct-from-patient tissue samples, which are becoming more common with the current surge in decentralized clinical trials (DCTs). The damage that can result from improper transport of these cells makes cold chain storage a crucial part of their handling.
As the cell and gene therapy space and other biotherapeutics manufacturers focus more heavily on these applications, the development of containers and shippers that can better facilitate ultra-cold storage has become a decisive driver across the industry. But for some more advanced therapies, the possibility of moving away from liquid nitrogen and toward dry ice and other materials is becoming increasingly feasible. Temperatures achievable with dry ice (up to -80 C°) will become more relevant as cell and gene therapies become more widely applicable for more patients; higher volumes of these therapeutics will drive more dry ice storage, which is often easier for facilities to achieve with existing equipment. Continuing to pioneer temperature-controlled shipping technologies that simplify the processes and materials involved is critical to creating efficiencies in a space rife with cost and complexity.
The Challenges of Liquid Nitrogen
When it comes to handling packages that require liquid nitrogen to maintain ultra-cold temperatures, there are a number of considerations that can create challenges for those handling these deliveries along a shipping chain. Applications that require liquid nitrogen are typically fitted with cryogenic storage dewars which are heavy, unwieldy packages that may be difficult for healthcare personnel or others to handle. Additionally, the temperatures achieved by using liquid nitrogen, as well as the liquid nitrogen itself, can be dangerous. For those unfamiliar with handling these types of shipments, the potential for frostbite or injury from direct contact with liquid nitrogen is very real, even during relatively short exposures. Extensive training, as well as personal protective equipment, is typically necessary to ensure the safety of those handling these shipments.
Another major concern relating to these types of shipments is connected to cost. The equipment necessary to facilitate these ultra-cold chain conditions is often highly expensive, and the nature of its use frequently requires a singular transport, which can be difficult to arrange logistically and can result in added expense. Because of the costs involved with both the payload and the materials needed to cryopreserve it, the vast majority of ultra-cold chain applications also require extra attention be paid to the chain of custody for these shipments. The overarching result is a shipping paradigm beset with complexity, cost, and potential danger.
As more temperature-sensitive biologics reach commercial acceptance, the needs of the industry will continue to shift with regard to cold chain storage. This push has resulted in short-term capacity expansion for many shipping companies and equipment suppliers, but it has also galvanized an increasing focus on the infrastructure and technologies necessary to simplify the requirements that accompany these types of shipments.
Enabling Simpler, Less Expensive Storage
Typically, the stringency inherent to the clinical trial setting will lead researchers to select the safest temperature range for a therapeutic in development, only to slacken those requirements once the drug is better understood and its ability to withstand a greater range of conditions has been verified. As the cell and gene therapy space continues to evolve, the characterization of these payloads is likely to result in a similar loosening of restrictions surrounding their storage. Working toward this eventuality from both a therapeutic development and container design standpoint is an important step in achieving compounding efficiencies in the cell and gene therapy industry.
Many companies have already begun this iterative evolution by trying to determine whether their advanced therapeutics can endure short-duration shipments using dry ice. While this has led to some data concerning the feasibility of this approach, more comprehensive insight into the method has been hampered by scale – many of the involved sites are comparatively small and lack the necessary infrastructure to allow for their own storage. This often forces shipments to remain in storage for several days prior to their use, a scenario best served by liquid nitrogen.
Although dry ice comes with its own complexities, its widespread use in cold chain storage for other therapeutics makes it a familiar part of the process for many healthcare professionals. Dry ice can enable cold chain storage between -50 and -80 C°. For applications that require lower temperatures, liquid nitrogen is the only option. For less stringent temperature requirements, companies may also utilize an active refrigerated shipping device, though these systems typically only reach -20 C°. Currently, some companies are exploring the potential for phase-change materials to bridge the gap between refrigerated systems and dry ice, which remains the most viable option for the temperature ranges that exceed refrigerated storage capabilities but fall short of requiring liquid nitrogen.
The Future of Cold Chain Shipping
Although the need for liquid nitrogen is likely to remain steady in the coming years, the bottleneck created by its complex handling needs will only worsen as temperature-sensitive therapies become more popular. This translates to issues related to the cost of these drugs; mitigating them will require a holistic approach that targets affordability along every point of a therapy’s development and commercialization. Doing so has widespread implications for patients, in terms of both affordability and accessibility, as many of these drugs are only approved for reimbursement as a treatment of last resort.
At this stage in the cell and gene therapy development pipeline, many of the treatments currently available are highly individualized. Autologous cell therapies, which utilize a patient’s own tissue in their formulation, require increased emphasis on temperature control for both the payload and the patient samples used to manufacture it. These treatments, which frequently cost hundreds of thousands of dollars, are also invaluable, given the intractable, life-threatening conditions they are designed to treat. The time lost in compromising a single dose, or an individual sample, can have devastating consequences for a patient.
Ultimately, the increasing need for ultra-cold storage, coupled with the challenges that accompany this trend, is driving innovation across the biotherapeutics space. By working to bolster capacity and advance simplified storage technologies for these drugs, biopharma companies, shipping companies, and container suppliers are pioneering a future that enables greater patient access to more affordable life-saving treatments.