The Importance Of Efficient Product Handling In The Pharmaceutical Industry
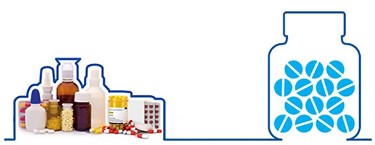
Effective Relief from Production Headaches
Total market demand in the pharmaceutical sector is expected to be close to $1.4 trillion by 2020, putting enormous pressure on manufacturers to meet ever-growing production schedules. Optimizing processes in order to make production more efficient is therefore a necessity, and a key element in achieving these efficiencies is to look closely at how products are handled on the production line to improve OEE.
Many pharmaceutical manufacturers are looking to processing and inspection equipment providers for solutions. Capital expenditure in equipment has been increasing by 13% year-on-year. The total spend in 2014 was in excess of $21.4 billion, which shows a willingness to invest in new technologies in order to stay ahead of the competition.
C3570 Pharma Checkweigher
Fiitted with numerous configurable options and features to meet the requirements of today's pharmaceutical production companies.
Why Is Product Handling So Important?
Handling products on high speed production lines presents a myriad of challenges. By identifying the problem areas and investing in appropriate solutions, the benefits and return on investment will be immediately apparent.
The smooth progression of packages along the line is the ultimate goal, and the more streamlined and efficient this process is, the greater the output you can achieve. The result is end products being produced cost effectively, without compromising on quality. Especially given that any product not running smoothly through the production line may have a very negative impact on efficiency.
Meeting The Challenges Of High Speed Product Handling
One common issue faced on pharmaceutical production lines is the misalignment of packs as they travel through the process. Allowing askew packages to continue down the line not only results in less accurate weighing but also leads to potential blockages and jams downstream.
Any unplanned downtime can have a costly impact on productivity. The C3000 Series Checkweigher from METTLER TOLEDO features advanced sensors in order to monitor package orientation, ensuring askew packages are either rejected or corrected automatically before continuing.
If product is not centred when it reaches the weighing conveyor then accuracy can also be affected. Transversal adjustment is a feature that automatically re-centres product, which leads to improved weighing accuracy and better positioning as items continue through production.
The Challenges Of Unstable Products
Stability is also a key area of product handling, as taller items with small footprints such as bottles and aerosols are prone to toppling over, which can also lead to unscheduled downtime. Vibrations need to be kept at a minimum and transition points between conveyor belts need to be carefully designed to ensure smooth product transfer.
The C3000 Series has a number of features to help reduce or eliminate these issues. Side belts are available, constructed using precision milled monoblock parts in order to reduce vibration and stabilize products during weighing, whilst high precision crowned rollers optimize conveyor belt guidance in order to increase product stability.
A separate conveyor and belt specifically for rejects also helps to eliminate possible vibrations caused by rejections, leading to highly precise and exact product transfer.
Detecting & Rejecting Cartons With Open Flaps
Carton line speeds are getting faster and faster and there is always a risk that some will have open flaps, which may damage printing devices, vision systems and sensors downstream if undetected, as well as cause blockages.
Product control options on the C3000 Series enable pharmaceutical production companies to configure their checkweighers to detect open flaps, rejecting them immediately in order to minimize disruption. In addition, as this is a configurable option, no additional space is required on the line, ensuring your manufacturing footprint is as small as possible.
Reducing Downtime Required For Changeovers
Changeovers can be frequent on pharmaceutical production lines. Ensuring quick, efficient product changes is critical to maintaining production schedules. For maximum process reliability, digital position control is available. It reduces the time spent on component adjustments and automatically controls article changes. The result of allowing this process to be controlled digitally is error free product changeovers, which leads to reduced waste and costs as the machine can only be started when all relevant parameters have been correctly adjusted.
Checkweighers have a pivotal part to play in pharmaceutical production, and by investing in the capability to handle products efficiently, through systems such as the C3000 Series, pharmaceutical manufacturers can maximize uptime, increase productivity and ultimately improve profitability.