The Pharma Design Detour: Addressing Shortcuts In Facility Design
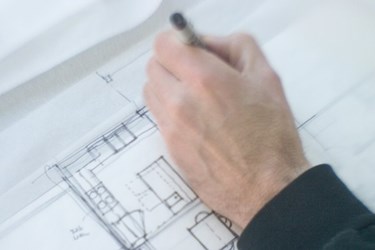
By Geoff Middleton
Introduction
Manufacturing facilities in the pharma industry may set the bar high for complexity and capital density when compared to the wider industrial community. It would be reasonable to assume that the design of such facilities would therefore be given the greatest possible care and thorough consideration. This is true for the process of developing detailed technical documents and specifications for the wide variety of equipment, materials, and systems necessary to construct such a facility. At the very beginning of the design process, however, where the initial concepts are developed and decided upon, all too often a sense of urgency overtakes, leading to shortcuts in the process. The results of these shortcuts are less efficient, more costly manufacturing facilities to construct, operate, and maintain.
The industry has been slow to perceive the costs of foreshortened initial design due in part to high profit margins, product-to-market urgency, and, after many years of practice, tradition. Two factors seem poised to change this pattern. Firstly, broad market forces from many sides are placing enormous pressure on operating companies to reduce costs and prices. Secondly, the shortened initial design process is widely perceived to have only incremental and insignificant effect on capital and operating costs. Several recent redesign efforts have convinced the author that in many cases the lost capital and burden to operations may in fact be substantial. Inefficiency of capital and operations we could overlook previously is rapidly becoming intolerable for the future.
Several areas of focus will likely need to be combined in order to break the current pattern. Early on, it may be practical to bring in expert outside forces to ‘pressure test’ early stage design work in order to be certain a thorough range of alternatives is evaluated. To address the current suboptimal design process in the longer term may involve changes to project delivery methodology, both within the capital projects departments of operating companies and the engineering companies that serve them.
The Pharma Design Detour
At the heart of the pharma design process detour is a dogmatic principal of design. The basic, initial design idea forms an unbreakable pattern that determines range boundaries for any project, including cost, efficiency, flexibility, performance, longevity, etc. for the design, construction, and operating life of the facility. Development then follows. Hence, traditionally, no part of the design process is given more care and thoughtful attention than the formation of the initial design scheme.
Many will have seen this concept chart of the relative influence of various stages of a project. It is no surprise that the earliest stage, where all the high level scope and solution decisions are made has the greatest impact.
Influence By Project Phase
The pharma industry has been affected by various forces that have led to systemic shortcuts in this initial design process; primarily the need for speed, and a perceived insensitivity to cost. The legitimate urgency of bringing a new facility on line to provide product to the marketplace has imprinted these behaviors on the industry.
There are also organizational and cultural influences in both the owner’s and engineer’s companies. Project procedures within many operating companies assign limited time and funds to concept design. At such an early phase of a project it may be uncertain that approvals will be forthcoming; hence, limited time and spending seems reasonable. The affect, however is the foreshortening of early design.
When presented with these limited funds for concept design, the engineering company views the activity as a loss leader. As it is only the most experienced and capable designers that can effectively develop the concept design, and as they are routinely quite expensive members of the staff, the obvious incentive is to limit the loss. This is done by allowing limited time and seizing on the first alternative that works to the satisfaction of the client, thereby bringing the phase and its losses to an end. Few responsible business owners would do differently.
In any case, the result has been short shrift paid to the development, comparison, and analysis of conceptual design options. All too often, the first concept that works is anointed as pattern for the life of the project.
Few other design spaces follow a similar, abridged process, and would not consider doing so in light of the costs and loss of efficiency involved. Offices, laboratories, schools, governmental buildings, institutional facilities, and industrial facilities in industries parallel to the pharma community uniformly exert rigorous development, analysis and challenge to design at the concept level, with full awareness of the consequence of short fall. In some instances, these other communities opt for rigorous peer design review or design competition in order to elicit wide ranging, imaginative design options.
The accepted wisdom in the pharma industry is that the trade of speed in design for thoroughness and quality of design has only incremental impacts on capital and ongoing operational costs. These hidden and lost costs generated by short cuts in design may in fact be significant. It seems clear in any case that the industry can no longer afford its unconventional design norms.
Organize For Success
Not surprisingly, organizations have developed to mirror our desired outcomes. Where schedule is king, capital projects departments within operating companies and the engineering companies that serve them have grown and organized with that goal in mind.
Pharma operating companies have project management, engineering, or realization departments that direct the design and execution of manufacturing capital projects. These groups have as success criteria that budgets and schedules are not exceeded. Note that uncovering an optimal solution is not front and center on the success criteria. Once capital is approved it becomes the target. To the objective observer, the larger the budget and longer the schedule the less likely failure becomes.
Engineering companies in the pharma manufacturing space are large, multi-discipline organizations that prosper by billing for thousands of hours. Once again, the larger and longer the project, the better. Additionally, moving the project out of the concept phase, in which a small number of highly paid experts is engaged, to the detailed design development phases that employ the hours-hungry army of engineers and designers is crucial to profitability.
Neither organization is structured or incentivized to find optimal design solutions, reduce budgets, or pursue aggressive schedules. They are structured to execute large complex projects without failure to achieve initial goals.
Culture
In many cases outside of the pharma industry, the development of the concept is separated from detailed technical development and construction. Expert firms focused solely on concept design deliver a carefully crafted concept to companies expert in detailed development, specification, and construction oversight. In other cases, parallel, independent, rigorous peer review and alternative development is engaged as a means of verifying and challenging a design.
One significant reason for this is culture. The type of professional adept at innovation in the blue sky environment necessary to develop high performing design work is rarely a match for the hard-driving, single-minded execution team. In a direct parallel from the pharma industry, we would not expect the scientists in research and development to exchange places readily with the operating staff of a manufacturing facility. Yet in our current capital projects organizational model, this is exactly what is done. The hard-driving, linear thinking that is crucial to project delivery has spread its culture to conceptual design.
Benefits
Clear benefits result from a superior design. Capital costs can be reduced. Schedule to first manufacture can often be reduced as well. Operating costs and the cost of goods are also likely to be positively affected. Ironically, a superior, elegant, and efficient initial design may well be completed in shorter time than the urgently adopted design, even including an extended concept period of painstaking options development and analysis.
Summary
It seems clear that numerous forces in the industry, the economy, and government are at present aligned in applying cost pressure on the pharma biologics industry. Further, these influences seem likely to be sustained or increase in the future. Value is currently squandered by abrupt and curtailed concept design efforts on the facilities that have the greatest impact on the industry’s cost of goods. The procedures that lead to this loss of value and negative impact on cost of goods must change. A return to conventional design norms is in order, as may be alterations to organizations involved in project delivery.
The rush to do so should never be permitted to outweigh thoughtful planning. It is, after all, the idea that counts!
Biography
Geoff Middleton is a process architect with over 30 years of programming and design experience in the Pharmaceutical, Biologics, and Regulated Industries, working for both Jacobs Engineering and Life Sciences International before starting cGMA in 2004 and IDEA2.0 in 2014. Geoff’s expertise is in early- stage decision making, feasibility studies, site selection, programming, master planning, and conceptual design.