The Role Of Human Performance Tools & Just Culture In Biopharma Operations
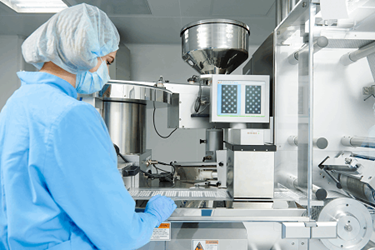
By Brad Rank, associate director of QA P&TT at Bayer Pharmaceuticals and member of the BPOG Human Performance Team
To be successful in the pharmaceutical and biotech industry, a company must find a balance between sometimes contradictory objectives — from product development, manufacturing, management, shareholders, and regulators, to name only a few. In this complex environment, we aspire to demonstrate control and competency to gain and maintain regulatory approval, deliver safe and life-giving medicines to the world, and maintain public trust.
In most cases, this complexity and risk is successfully managed, and the business is sustained and grows. However, failure and losses are part of doing business. These losses and failures can be related to compliance issues (warning letters, consent decrees), operations (product write-offs), supply chain (recalls, shortages, failure of on-time delivery), as well as others. How can companies manage possible failures and losses to minimize risk and produce at maximum efficiency?
The behavior of the people within an organization can be the least predictable part of the business. While the industry has been successful in incorporating lean and Six Sigma principles to increase operational and system efficiency, there has been a lack of similar gain demonstrated when dealing with human behavior and human error. According to a survey conducted by the BioPhorum Operations Group (BPOG) Human Performance Team, industry members report that nearly 40% of deviations are attributed to human error. Why is this so? It would be easy to conclude that it is the people involved in the incidents who are to blame.
Despite the best efforts and intentions of those involved in root cause analysis, if people are ultimately blamed for these failures and losses, most likely the recommended solutions will not correct the problems or prevent recurrence.
As the famous Henry Ford saying goes, “If you always do what you’ve always done, you’ll always get what you’ve always got.” If you are stuck in this loop, there is probably something missing in all of the efforts you’ve tried to date — namely, establishing a culture that is just, adopting human performance tools, and driving fear out of your organization.
The Impact Of Fear
Fear is not a word commonly discussed in corporate America, much less in a technical industry such as biopharmaceuticals. Whether we like to admit it or not, however, fear can have a large influence on the behaviors of people in your organization, and on your organization’s culture. There is fear of regulatory authorities, fear of a boss, fear of failure, fear of harming a patient, fear of lost revenue. The emotion of fear, in itself, is neither a good or bad thing; however, I do believe that when left unexamined or unrecognized, responses to fear can be detrimental to the business.
An example is fear that causes an organization or individual to slow down and be careful. This uneasiness results in caution and calculated responses. For instance, when performing a critical step and knowing that a mistake would have a significant loss of product, you double check your work, or you stop and ask a question if you are unsure. In a larger sense, there is a shared industry understanding that what we produce impacts people’s lives, and that utmost care must be taken to ensure that our products do not negatively impact people’s well-being.
Detrimental responses to fear can lead to a paralysis of action, for instance. Fear of failure can manifest itself as an individual that escalates every decision or avoids performing critical steps. An organization’s fear of regulatory agencies may require corrective and preventative actions (CAPAs) for every deviation, regardless of criticality and limited resources. People who fear for their job security may manipulate key performance indicators (KPIs) in an effort to look good to management. On an industry level, fear may have the unintended consequence of making us overly risk averse and limiting innovation. However, the most detrimental fear, I believe, occurs in the context of relationships, leading to a lack of communication, decreased honesty and trust, and, at worst, anger and resentment.
We all have experienced fear at one time or another, and I think we can all agree that people prefer to feel safe and secure. In industry we build systems, routines, policies, and procedures to mitigate risk and maintain some level of control and security. It is logical and easy to believe that as long as we follow all of these controls, a positive outcome will occur. Given this philosophy, when something goes wrong, it is also reasonable to think that the systems put in place to protect us aren’t to blame, but rather the people who improperly use the systems.
In the history of medicine, there have been a heartbreaking number of incidents that resulted in death or injury. In fact, the foundation of our current regulations are based on these tragic events, and I believe that regulation — and audits related to these standards — are necessary and critical for the industry. The fear of legal and other consequences does help the industry harmonize and protect patients. As a result of these regulations, we are much less likely to hear about or be affected by an incident in biotech as severe or tragic as those seen in the past.
However, our reliance on these systems can lead to a culture of compliance for compliance’s sake. In addition, there can be a disconnection from the foundation and rationale of why these regulations and systems exist in the first place. I suggest that this model is limited for addressing the issues that the industry faces today.
Benchmarking Against Other Industries
The airline and nuclear power industries have also experienced tragic incidents in their history: Three Mile Island, Chernobyl, US Airways Flight 1549 (which landed in the Hudson River), and others. The impact of these tragic events helped fuel research into why things go wrong and how to minimize risk.
Over the past few decades these industries have transformed by challenging traditional management and regulation strategies to implement a culture that is just and that focuses on human performance. How can you ensure employees respond well in critical moments? Do employees know what the critical step is in a given process? What safeguards need to be put in place? Do employees feel free to report any/all issues? There is a shift away from blaming people towards better understanding how culture and systems influence individual behavior — and how that relates to failures.
This paradigm shift towards examining the dynamics of why things go wrong at the systems and organizational level, rather at the individual level, has been significant in better understanding failure. Fear must be driven out of a company culture.
The Marks Of A Just Culture
A fear-based culture can create an environment where people are not forthcoming with information that may be crucial to avoiding accidents. Transparency creates a culture where information that might save the next lot, avoid errors, or improve KPIs is readily available. In general, moving away from a fear-based culture can increase reliability, sustainability, and safety.
Some signs of a just culture are:
- People at all levels are held accountable to their appropriate culpability.
- Management understands that people can make imperfect systems work through competence and strategic problem-solving approaches.
- Management makes the effort to understand how the work is actually performed, rather than how they imagine it works.
- Management encourages open reporting and focuses on building confidence and competence.
- Measures are taken to encourage and facilitate behaviors that add value — and to manage and coach employees whose behavior does not add value.
A just culture isn’t fear–based; rather, it embraces learning and mature risk-based thinking, including the risks posed by human behavior. A just culture is one where compliance isn’t just a goal unto itself, but is an output based on fundamental principles of human performance and competence that are encouraged, engrained, and reinforced into the workforce.
Basic Principles Of Human Performance
The following principles serve as the foundation of human performance:
- People are fallible, and even the best make mistakes.
- Situations that lead to errors are predictable, manageable and preventable.
- Individual behavior is influenced by organizational values and processes.
- Achieving high levels of performance is based largely on the encouragement and reinforcement received from leaders, peers, and subordinates.
- Understanding the reasons why mistakes occur and applying the lessons learned from past events can prevent future events.
These principles help establish a culture focused on learning and solving issues before they become a problem, and learning from past problems to avoid future ones. I suggest that the understanding and application of a just culture and human performance best practices is the key to our industry taking the next steps to greater reliability, competency, safety, and growth.
Conclusion
The principles and philosophy discussed above have demonstrated their efficacy in the nuclear and aviation industries, as well as in the military. Companies that have started implementing some of these principles have seen a drop in deviations and errors.
Are the pursuit of a just culture and the adoption of human performance principles worth it? The industry is changing, competition is growing, global complexity is increasing, and the need for highly reliable and sustainable production is needed now more than ever. Each company and individual must decide whether it is worth investing the time and effort to continually improve upon its current processes for better results and quality.
Changing a company culture takes the courage to think and act differently — to alter how we manage ourselves and our people, how we investigate and deal with deviations, how we apply and respond to regulatory agencies. It takes a willingness to review and change the very systems, policies, and procedures that we think are providing control and safety.
Recommend Reading
- Sidney Dekker, The Field Guide to Understanding “Human Error” – 3rd Edition, CRC Press (Boca Raton, FL), 2014.
- Sidney Dekker, Just Culture: Balancing Safety and Accountability – 2nd Edition, Ashgate Publishing Company (Farnham, Surrey, UK), 2012.
Acknowledgements
The author would like to give special thanks for review and edits to Gerry McAuley and the BioPhorum Operations Group Human Performance Team.
About The Author
Brad Rank has 17 years of experience in the pharmaceutical industry at companies such as Merck, Wyeth, Johnson & Johnson, and Bayer. In that time, he worked in various roles including manufacturing sciences, validation, and quality, supporting development, upstream, downstream, and SFF production. He currently works as an associate director in pharmaceutical divisional quality at Bayer Healthcare.
About The BioPhorum Operations Group (BPOG)
The BioPhorum Operations Group’s (BPOG) mission is to create environments where the global biopharmaceutical industry can collaborate and accelerate their rate of progress, for the benefit of all. Growing from an end user group in 2008, BPOG now comprises 45 manufacturers and suppliers deploying their top 2000 leaders and subject matter experts to work in six focused Phorums, articulating the industry’s technology roadmap, defining the supply partner practices of the future and developing and adopting best practices in drug substance, fill finish, process development and manufacturing IT. In each of these Phorums, BPOG facilitators bring leaders together to create future visions, mobilize teams of experts on the opportunities, create partnerships that enable change and provide the quickest route to implementation, so that the industry shares, learns and builds the best solutions together.
Disclaimer: This article reflects the personal opinion of the author, and does not necessarily reflect the views of Bayer.