This Takeda Official Thinks Pharma 4.0 Won't Be Optional Much Longer
A conversation with Gunter Baumgartner, Takeda
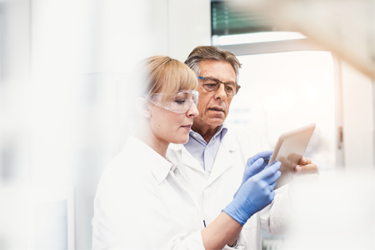
Not so long ago, biologics and pharma manufacturers got along just fine without the internet, not to mention a high-speed connection. Now, business grinds to a stop without it.
Like high-speed networks, experts who once called advanced technology an unnecessary advantage now see the use of artificial intelligence and automation as an impending necessity to do business. Resist at your peril.
Gunter Baumgartner, Takeda’s global head of engineering, plans to speak about how the company is leaning into the technology when he presents at the 2024 International Society for Pharmaceutical Engineering (ISPE) Annual Meeting & Expo. ISPE trademarked the term Pharma 4.0 and created an initiative to help companies incorporate more digitalization and automation into pharmaceutical manufacturing.
Ahead of his talk, we asked him for a preview with some specific questions about the challenges that come with integrating complex new technology.
Pharma 4.0's architects wrote that it's "not a must, but a competitive advantage." How is that notion holding up? In other words, are digital ecosystems becoming more like must-haves — less like should-haves?
Baumgartner: I would like to quote Christophe Weber, our CEO, from his annual letter to shareholders where he outlined Takeda’s digital ambitions:
“Embracing cutting-edge technology, including AI, and seamlessly integrating data-driven insights into our business operations opens up exciting possibilities for better, faster and more efficient execution.”
This vision drives all our Pharma 4.0 initiatives within the manufacturing network. It’s becoming increasingly clear that the pharmaceutical industry will soon be divided into two groups: those that have fully embraced the digital transformation and those that have gone out of business. Thus, digital ecosystems have indeed transitioned from being “should-haves” to “must-haves.”
Interoperability seems like a key component of this movement. Describe the current challenges with standardizing digital technologies and getting them to talk to each other.
Baumgartner: Interoperability is indeed a crucial aspect of this digital transformation. The primary challenge we face in standardizing digital technologies and facilitating their interaction is the diversity of legacy systems across our manufacturing sites. Takeda has evolved over the years through a series of significant acquisitions, one of the largest being the integration of Shire in 2019. In the manufacturing network, two of the biggest challenges are enterprise resource planning (ERP) and manufacturing execution systems (EMS).
Takeda and Shire had different technical solutions. The problem was twofold: deciding which system to use as our future “north star” and how to handle the legacy systems. In these situations, deciding happens on a case-by-case basis. While in some instances it might make sense to keep different systems running in parallel, at least for a transition period. In other cases, a fast harmonization might be more appropriate.
This was a pivotal moment in our history and marked an exciting progression in our transformation journey. However, as we continue to grow, so do the landscape and the technologies we utilize. The products and technologies we select today may become obsolete within a year — we have witnessed such instances. Hence, the speed of implementation is of utmost importance. Achieving standardization across a manufacturing network of over 25 sites while simultaneously implementing swiftly is a daunting task. To tackle this, we strive to strike a balance between global and local responsibilities.
Our goal is to develop strategies on a global scale with local accountability for on-site implementation. This approach aims to ensure that only compatible local digital technologies are deployed, ultimately enabling them to communicate effectively with each other.
What would you say to a project lead who's reluctant to risk investing in and validating novel technology?
Baumgartner: I understand the hesitation to invest in and validate novel technology due to the inherent risks and uncertainties, especially in a pharmaceutical environment where patient safety is our highest priority. However, it's important to remember that innovation is the driving force behind progress in any industry, including ours.
While new technologies may pose challenges in the initial stages, they often open up opportunities for efficiency, cost reduction, and competitive advantage in the long run. Our investment in novel technology is not just about the technology itself. It's about creating value and, most importantly, better serving patients.
We need to approach this from a risk management perspective rather than avoiding risks altogether. This involves conducting thorough research and feasibility studies, piloting the technology on a smaller scale before full implementation. Moreover, our vision is to embrace cutting-edge technology as part of our digital transformation journey. This is not just about staying current, but about leading in our industry. Therefore, I would encourage the project lead to view this not as a risk, but as an opportunity for growth and leadership. Remember, the greatest risk in today's fast-paced digital world is not taking any risks at all.
What digital technology are you most excited about?
Baumgartner: As the head of engineering, my focus is primarily on the application of digital technology within manufacturing. As stated in our annual integrated report:
"By transitioning from manual to automated processes in many of our manufacturing operations, we’re improving efficiency and quality and allowing our employees to focus on other value-add tasks. We aim to be 80% paperless in our manufacturing organization by the end of fiscal year 2026."
And we have already implemented a system that eliminates 100% of paper from the validation life cycle in our more than 25 manufacturing sites.
Two technologies that I'm particularly excited about are automated visual inspection (AVI) and manufacturing execution systems (MES). AVI technology has the potential to eliminate the need for manual inspection of millions of vials and ampoules, significantly increasing efficiency and accuracy. On the other hand, MES allows us to transition from paper batch records to fully electronic batch records, which is a critical step towards achieving our vision of "one-day batch release."
These technologies not only enhance our manufacturing processes but also align with our commitment to digital transformation and patient-centricity.
How do augmented and virtual reality fit into this story?
Baumgartner: Augmented reality (AR) and virtual reality (VR) play a significant role in our digital transformation journey. We have been extensively using AR/VR for training purposes across our manufacturing sites. This innovative approach contributed to us receiving a "Facility of the Year Awards" Overall Winner Award from the ISPE in 2022. In addition to training, AR is also being utilized for maintenance on production lines.
This became particularly useful during the virtual site acceptance tests (SATs), when COVID-19 travel restrictions prevented vendors from visiting our production sites. The use of AR enabled us to conduct these tests remotely, ensuring that the commissioning and start-up of a new facility could proceed without delay.
Looking ahead, one of our key digital initiatives is the development of digital twins. A digital twin is a virtual replica of a physical system, allowing us to simulate, predict, and optimize the system's performance. This technology will enable us to further enhance our manufacturing processes, reduce downtime, and improve product quality.
In summary, AR/VR technologies are not just enhancing our current operations, but they are also paving the way for future innovations. They are integral to our commitment to harnessing the power of digital technology.
Pharma was talking about using AI and ML years before ChatGPT stunned the world. How have large language models and their explosion into the public conscience changed things for AI in pharma?
Baumgartner: In manufacturing and quality control, Takeda is harnessing AI and ML to enhance production quality and efficiency. For instance, we're conducting proof of concepts using these technologies for risk classification and deviation summaries. This will speed up the management of deviations and investigations that may occur during the manufacturing process. After thorough testing, we plan to expand these capabilities across sites within the next few years.
In the supply chain, we're using AI and ML to boost cost-effectiveness and process sophistication. A key part of this is our digital twin approach to distribution and logistics, which lets us model complex logistics network configurations to find the optimal balance of multiple factors.
We're also supporting our expansion of data, digital, and technology with a comprehensive rethink of infrastructure and training. This includes developing insourcing capabilities with Innovation Capability Centers (ICC), our “digital factories” where we develop our own digital capabilities to reduce our reliance on external partners. By the end of our fiscal year 2024, we will have opened four ICCs.
We recognize that skill development is integral to our strategy of capturing the full potential of digital and AI. We are expanding the skills of our people in current roles, introducing new skills for new future roles, and re-skilling to prepare for the sunset of outdated roles. At Takeda, more than 27,000 employees are engaged in digital learning, including 4,000 who have completed training to gain knowledge of robotic process automation (RPA), which allows us to streamline our operations and improve efficiencies.
What have the last five years or so taught you about moving famously change-resistant industries away from legacy systems?
Baumgartner: The past five years have been a transformative period, especially for traditionally highly regulated industries like pharmaceuticals. The industry has come to understand that digital transformation is not just a trend, but a necessity for survival and growth. Legacy systems, while reliable, often lack the flexibility and efficiency needed in today's fast-paced, data-driven world.
Transitioning away from legacy systems involves risk, including operational disruptions and security concerns. However, the industry has learned to manage these risks by adopting a phased approach to implementation, rigorous testing, and robust cybersecurity measures.
Resistance to change is often due to a lack of understanding or fear of the unknown. Therefore, investing in comprehensive training programs and effective change management strategies has proven crucial in helping employees adapt to new systems.
Many pharmaceutical companies have successfully accelerated their digital transformation by partnering with tech companies and startups. These collaborations bring in fresh perspectives and advanced technical expertise.
Lastly, the ultimate goal of digital transformation in the pharma industry is to improve patient outcomes. Whether it's using AI to accelerate drug discovery or leveraging data analytics for personalized medicine, the focus is always on creating value for patients.
The journey away from legacy systems is a complex, yet necessary, endeavor. The lessons learned over the past five years will undoubtedly guide the pharma industry as it continues to navigate the path of digital transformation.
About The Expert:
Gunter Baumgartner is global head of engineering at Takeda Pharmaceuticals International AG in Zurich with responsibilities for the company’s global capital expenditures portfolio, automation and MES strategy, maintenance, and all engineering support for Takeda’s 30-plus manufacturing network sites. He is also an active member with ISPE. Previously, he led a four-year greenfield project related to new sterile liquids and solids manufacturing plants in Russia. Before that, he held various management positions at a biologics and pharmaceutical manufacturing site in Austria. He has been a member of ISPE since 2005 and is a past board member. He holds degrees in general management from the University of St. Gallen and the Henley Business School. He also has a degree from TU Graz.