Training Production Operators In Aseptic Technique: Common Pitfalls & How to Avoid Them

By Paula Peacos, ValSource, Inc.
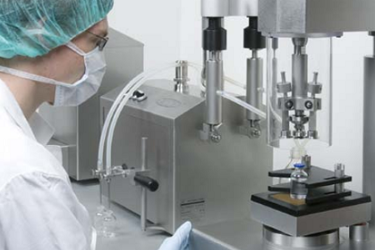
Good, robust aseptic technique is critical to achieving successful contamination control during manufacture of aseptically processed products. Proper execution of aseptic technique is a skill that requires detailed, in-depth, targeted training and demonstrated proficiency. Firms that utilize aseptic technique as part of their contamination control strategies go to great lengths and expense to develop and provide robust in-house training programs, procedures, and/or work instructions to ensure that production operators can efficiently and effectively employ aseptic technique. Operators train on the pertinent procedures, frequently attend additional classroom or computer-based training, and are often required to physically demonstrate proficiency before permission is granted to work on the processing line. Yet poor or improper aseptic technique is one of the most commonly identified root causes for microbiological data deviations. Retraining an operator involved in a microbiological excursion is almost always part of the corrective and preventative action (CAPA), yet repeat excursions and deviations due to improper aseptic technique still routinely occur. So, why do some operators still have difficulty executing the task after completing such intensive training programs?
Are You Really Reaching Your Target Audience?
To the average production operator, especially one who is new to the industry and working in an environment where cutting edge technology is everywhere around them, it is difficult to comprehend why one of the most critical job functions in the production environment involves the use of a mop and bucket. This is because many production operators have little or no formal technical background or practical training in basic microbiology.
Some firms try to mitigate this by providing basic microbiological training that is specifically designed for the non-microbiologist. Such training modules generally provide an entry-level introduction to the most common types of facility microorganisms, their sources, how they grow and reproduce, and how they enter a facility and pose a contamination risk to the manufacturing process and product. They discuss the importance of contamination control measures such as good gowning practices, cleaning and disinfection, and environmental controls. The principles of environmental monitoring and how it is performed, the associated regulatory requirements, and the risks that a contaminated or adulterated product could pose to patients are also covered.
While all of this is information that the trainees need, in many cases it is presented in a manner that is better suited to entry-level analysts in the microbiology lab. The content needs to be presented in a way that is easily understood and assimilated by the target audience. For the average production trainee, the key is to deliver the information in practical terms so that the subject matter becomes as tangible and “real” to the trainees as possible. The more the trainees can relate the information to aspects of their daily life both in and out of the workplace, the easier it is for them to apply the principles on the processing line.
Are You Delivering The Right Message?
The training module must emphasize the fact that most effective contamination control is achieved by exclusion. It is far more effective to proactively prevent the ingress of microorganisms into a facility than it is to remove them once they have gained entry. It is not uncommon for production operators to assume that thorough cleaning and disinfection will surely remove any microorganisms present, that environmental monitoring will effectively detect any and all organisms present, and that that the microbiology laboratory will surely detect any contamination during product testing. Consequently, it is necessary for the training content to address the limitations of our existing microbiological and contamination control methods.
It's All About Ownership
It is also critical to emphasize the importance of the production operators’ individual roles in effective contamination control. Their diligence and skill in executing their job functions properly and with strict attention to detail will determine the success of failure of any contamination control program. Each individual working in the production environment must assume individual ownership. It is also critical for operators to be able to apply the basic contamination control principles throughout the entire manufacturing environment, not just in the area in which they execute their specific job function. If an operator does not thoroughly understand the components of the contamination control program and its limitations, they will often fail to recognize a contamination risk that is right in front of them. An operator who takes ownership is more likely to recognize that risk, which then enables them to become an active part of the continuous improvement plan for the contamination control program.
Not All Trainers Are Created Equal
It is essential to employ the right trainer. Experienced operators are commonly tasked with training less-experienced operators. However, there are two pitfalls with this approach that must be avoided. First, experience is not always the best teacher. A potential trainer’s individual ability to train should also be assessed. They must possess the ability to relate information clearly and accurately, as well as be able to confirm trainee understanding. More importantly, they need to be able to recognize the signs that the trainees are not understanding — and adjust the communication of information accordingly — during delivery. Simple transmission of information alone is often insufficient.
All operators must be trained to perform tasks in the same manner. When operators train other operators, there is natural tendency to pass on tips and conveniences they themselves have learned (e.g., “this is how I do it”). This happens most commonly when procedures are not specific or clear enough and allow for personal interpretation. Variations in procedural execution can cause variations in outcomes, depending on the procedure in question. When a microbiological data deviation occurs, such variations in aseptic technique can be difficult to identify during root cause analysis, especially as most investigations deal with events occurring in the past. The likelihood of such an occurrence increases with the number of trainers
Training The Trainers
In order to ensure that the intended information is delivered clearly and consistently, many firms institute training programs for their potential trainers. Such programs often involve classroom training on topics such as communication and presentation skills, confirming trainee understanding, etc. — followed by a demonstration of proficiency. Sometimes trainers are also required to attend a session of the presentation they are to deliver. Structured, standardized, on-the-job-training guides for trainers can also help ensure the information is delivered in a clear and consistent manner. The benefits of this are twofold, as the firm ensures (1) a truly effective training program is in place, and (2) that in-house trainers are appropriately trained, which provides sustainability for program. The all-important end-result is a reduction in the number of microbial data deviations and batch failures due to improper aseptic technique, and an associated increase in patient safety.
About The Author:
Paula Peacos is a senior consultant with ValSource, Inc. She has over 25 years of industry experience as a microbiologist, working for contract manufacturing organizations as well as small, mid-size, and large pharmaceutical organizations. Peacos has extensive experience in aseptic processing, API/drug substance manufacturing, cell therapies, nonsterile production (both clinical and commercial), microbiological laboratory management, and performing compliance audits internationally. She is an experienced trainer and has developed and implemented customized developmental and remedial programs. Peacos has also published articles and delivered presentations at industry meetings on topics such as risk assessment and using microbial recovery rates for trending analysis. You can contact her at ppeacos@valsource.com.