Vision System Inspects Pharmaceutics and Optimizes Production
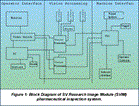
Contents
System Architecture
Modular Approaches Solve Problems
In the pharmaceutical industry, product tracking is crucial to meet government regulations as well as provide the data necessary to boost production line efficiency. SV Research (Harrisburg, PA) has developed a modular pharmaceutical inspection system that can inspect pharmaceutical containers as well as capsules and liquids while providing data crucial to optimizing production lines. More than meeting the needs of a conventional visual inspection system, the system is fully network compatible with an upgrade path that makes the most of technological advances without requiring new FDA and European CE Mark approval.
System Architecture A typical system architecture uses a PC host connected to one or more SV Image Modules (SVIIM) through a 100 base-T Ethernet, or in many cases the Alan-Bradley Data Highway Network. The SVIM was originally designed to be the second-generation replacement for the Alan-Bradley's CVIM system. The SVIM's connect to various cameras through off-the-shelf PCI-bus framegrabbers from Matrox (Dorval, Quebec), Coreco (St. Laurent, Quebec) or Cognex (Natick, MA)
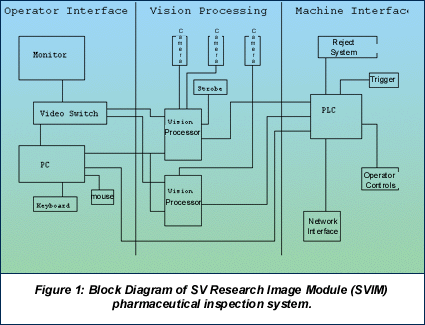
Each SVIM can accommodate up to eight camera stations containing one to three color or monochrome cameras with a maximum of 18 cameras. The front of the SVIM box provides 24 optically isolated Snap I/O connectors from Opto 22 (Temecula, California) for easy access to camera, trigger, lighting, PLC and discreet device controls and responses.
These connectors can accommodate eight 5 or 30 vdc input signals across standard shielded cable and 16 5 to 30 vdc output lines. The field lines come into a off-the-shelf digital I/O board plugged into the SVIM backplane and accessible from the module's front panel. "This way it does not have to come through a D-shell. D-shell's are not CE Mark qualified for these voltages," says SV Research's President Ron Lawson.
Up to eight SVIMs can be networked to a single PC, which contains the operator interface and front-end software package. An embedded Windows NT operating system in the SVIM provides both symmetrical processing on the twin Pentium II (350 MHz) microprocessors and a compatible environment for machine vision software libraries from framegrabber manufacturers such as the Coreco Sapera and the Matrox's MIL libraries as well as SVResearch's front end software. In this way, the inspection points are made locally, with full reportability along the network connection back to the central archiving and reporting PC.
Each SVIM has a USB and Ethernet board in addition to a digital I/O board to communicate with the operator interface on the host PC and any other plant network. In this way, different product lines can be downloaded to the PC from a central core and then passed on to each SVIM.
According to Lawson, the PLC's keep track of the overall inspection details such as pass/fail numbers and types of defects and these are passed back through the data network to the PC for archiving and reporting. Because the processing is done at the SVIM, the PC itself does not require a lot of power or computing strength. "Any commercially available PC will do as host," Lawson says.
Another part of SVIM's allure, according to Lawson, is the SVObserver front-end software package, a fully configurable operator interface that draws upon the strengths of software libraries without the need for any C programming knowledge. System configuration is a matter of "point and click" for the operator, giving quick access to a large range of stored products and standard quality checks; windows-based operations such as image and blob analysis, edge detection, feature measurements; logic and math functions; and image manipulation techniques such as Laplace filters, rotation, image subtraction, scaling, masking, rotation, thresholding, and 3x3 or 5x5 kernel definition.
Using microprocessor upgrades as the path to faster performance while keeping software standardized offers important benefits to government regulated industries such as pharmaceuticals and even food inspection.
"The pharmaceutical industry has strict requirements for machine processor and software validation with strict system change requirements and procedures," Lawson explains. "If you have a system that is currently functioning and need to add one more camera or framegrabber, you don't do that without modifying software, and that would require revalidation and testing. By using a dedicated 4-channel asynchronous [frame grabber] card, it allows us to have a dedicated upgradeable module that doesn't have a CD or floppy for software upgrades⦠And every time the Pentium improves, it gives us performance improvements without changing our application software, which has already been tested and validated. All we have to do is revalidate the hardware."
Modular Approaches Solve Problems With this architecture, Seidenader Maschinenbau can install multiple SVIM's to perform different inspection checks, take action based on pass/fail parameters through attached PLCs and report the data back to a central network.
The versatile modules can also check different packages and product lines -- such as capsules, vials, syringes, tablets, and ampoules, among others -- thanks to stored product libraries that are easily generated through the front end software. A particular application recently installed by Seidenader for injectable pharmaceuticals/vial inspection. In this scenario, the SVIM system checks for both cosmetic faults and contaminants in the injectable fluid.
Initially, the vials are fed single file from mechanical trays into a star wheel where each vial is separated in a single "spoke" of the wheel. The vials come into the first inspection area at line speeds of 100 to 600 vials per minute.
The first check insures that the liquid container has been sealed properly. If the seal is broken or inadequate, the defective vial can be separated before it has a chance to leak on good product or production machinery. This particular application calls for checking a metal cap and the crimp at the bottom of the cap over a glass lip. The operator, with the use of SV Focus software interface, chooses the type of cap, the type of seal (a crimp in this case), the proper height of the cap (a compressed rubber stopper lies under the cap and therefore the height of the cap assembly is indicative of a proper seal), and any other factors for the first inspection station, such as a color coded seal on the top of the cap, which can indicate content type.
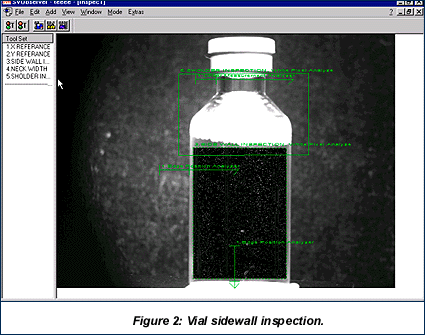
Depending on the product line, each inspection station may use a single camera, and rotate the product, or multiple cameras. According to Lawson, a standard cap inspection requires from three to six images around the circumference. Typically, the SVIM uses an RS-170 camera and requisite cable to convey an image of the vial to a four-channel asynchronous framegrabber. No preprocessing is done on the framegrabber for validation reasons stated previously.
A ring light above the vial casts an even harsh light downward. The cameras are placed orthogonal to the vial so they have a good view side view. By varying the angle of the camera and the cap, a sharp line around the crimp will indicate that the crimp surface continues beyond the half-way mark (45° in relation to the light), and represents a tight seal. Simple thresholding isolates the bright reflection and the line is checked for length and consistency to insure that the crimp is unbroken around the cap's circumference; a nine-pixel kernel for edge detection across the vertical surface of the cap checks the cap's sides for rips and tears.
Vial inspection continues with the glass bottle itself. Software running on the SVIM analyzes a pattern placed behind the glass vial. If the pattern behind the glass shows distortion caused by cracks or other defects, edge detection analysis in conjunction with operator set levels of acceptable distortion will reveal the problem. In the event that the distortion exceeds the operation set limits, the SVIM sends a signal across 24-V optically isolated lines to the PLC which increases its defect counter by one and conveys the vial to the defect bin.
SV Research uses lighting and optics to its greatest advantages, switching out optical modules as needed to meet each specific application. Pharmaceutical inspection also requires a full range of image analysis tools, such as blob analysis to check for glass shards in effervescent liquids. (Bubbles are uniform in size in liquids, while contaminates will vary in size.) The SV Research system is designed to meet FDA requirements that state an inspection systems must be able to detect contaminants in excess of 50-microns in diameter.
According to Lawson, SV Research believes that multiple processor speeds offer the development path and speed required to meet these stringent inspection requirements while keeping line throughputs high. "The speed that we take the images are based on line speeds, product, container size, fluid dynamics, etc," Lawson explains. "We've used as few as two camera images and as many as 10. These inspections are done several times throughout the inspection systems. Sometimes we stack the cameras to get a larger field of view while maintaining that minimum resolution. Whatever the customer needs, we can meet them."