What Is the Industry Underestimating About An ADC Supply Chain? – Part 2
By Trisha Gladd, Editor, Life Science Connect
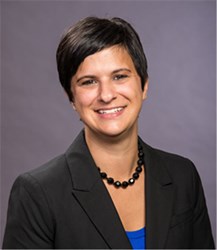
In What Is the Industry Underestimating About An ADC Supply Chain? – Part 1, I spoke with industry experts from Seattle Genetics, Lonza, and Marken about the various challenges an ADC supply chain can present, including longer-than-expected timelines and a lack of qualified facilities. In this article, Dan Bell, vice president of regulatory compliance and technical affairs for Marken, discusses regulatory challenges, and both he and Nathan Ihle, Ph.D., VP of CMC Strategy and Management at Seattle Genetics, offer best practices to apply when planning your ADC supply chain.
New And Unwritten Supply Chain Regulations Pose Supply Chain Challenges
Bell, a licensed US customs broker and certified customs specialist, is also responsible for trade compliance at Marken. He says that because ADCs are so relatively unknown in many countries, any regulations are fairly new. In some locations, Bell says the regulations may not even be written yet, and for those who do have regulations, lack of communication and confusion around compliance among countries is hampering transportation of the drugs.
“Most of the challenges are based on where the product is made,” he explains. “If manufacturing takes place in a large country with multiple jurisdictions or a region, such as Europe, with many different countries, different regulations will exist regarding how the very same material should be handled. Sometimes moving within a region or a multi-state country can be just as challenging from a regulatory perspective as moving internationally between foreign countries. There really is no good harmonization between the regulators right now.”
Because ADCs are not the typical biologic, companies working with ADCs should be prepared for specific challenges from regulators. “The release testing that needs to be executed on the ADC is unique,” explains Rohrer. “It contains both elements of large and small molecule analytical methods, so that is a bit of a challenge. Also, the facilities for manufacturing are typically dedicated to cytotoxins but are multi-use facilities, so cleaning and facility changeover are critical activities of interest to regulatory authorities. These are all areas that have to be well covered by any CMO expecting to compete and deliver product to clients in the current environment.”
So How Do You Prepare?
Bell explains that one of the most important things to do when mapping your ADC supply chain is to complete a risk assessment that includes feasibility. “If your commercial team has decided that perhaps it makes more sense for you to manufacture your product in China, for example, and you want to have it packaged somewhere else, like Canada, and then distribute in Europe, you are creating a really long and complex supply chain,” he says. “With each level of complexity, it gets harder to control certain logistics elements. Where stable, small molecules are pretty straightforward to store and transport, it's a little more challenging when you get to biologics. Additionally, because of the cytotoxin, you also have the issue of moving something that would be considered dangerous goods.”
He adds that because ADCs are highly-specialized products with only a small amount moving around the supply chain, most early studies don’t even cross a lot of borders. “This is why it’s so important to assess the risk you may encounter in your own supply chain,” says Bell. “Performing a risk assessment in the beginning allows you to determine upfront what your challenges along the supply chain will be.” The longer the supply chain, the harder it can become to control certain elements, so Bell says you have to make sure you design a supply chain to be scalable. “When you’re just sending a very small amount between the labs or you just have one or two clinical sites in the country, that’s fairly manageable. It’s when you have to scale up to production and distribution that it becomes very difficult to switch manufacturers or switch around how you're going to store and distribute it.”
In his experience, Bells says most large pharma companies will look to have a centralized control approach with a standardized process and then work with one partner on the supply chain side that will coordinate all those other players. “They try and simplify the process, in order to have very clear and written procedures and the smallest number of handoff points as possible. All of that really helps with ensuring GDP (Good Distribution Practice) compliant temperature control with the trade compliance, and it ensures they have a solid plan based on a thorough risk assessment in order to avoid sleepless nights.”
Working with multiple partners can certainly present a challenge, but like Bell, Ihle also believes these risks can be mitigated with proper planning. “It’s important to work with internal customers to have a clear picture of the likely demand for a product. How much will be needed for clinical studies? How much for commercial sales? What is the timing for the demand curve? What are the quality requirements at each point in a product lifecycle? Having as clear a picture as possible will allow for realistic production planning,” he explains. “With this information, intelligent choices can be made about batch size, selection of facilities, and staffing levels.” He says selecting an appropriate supplier is critical. “A good CMO must have the capacity and technical capabilities that the product requires but also must have a good cultural fit,” says Ihle. “Alignment of expectations with respect to communication and decision making and a good quality culture are important for the long-term success of a manufacturing relationship.”
So while the development and manufacturing of an ADC can be difficult, it certainly isn’t impossible with proper planning and the right partner(s). And with the ADC market projected to be worth $10 billion annually by 2024, it’s certainly worth the effort.