When Glass Vials Fail At Low Temperatures, Consider A Cyclic Olefin Polymer System
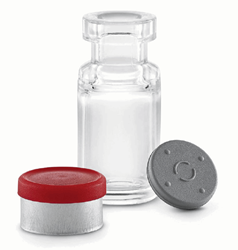
By Whitney Winters, West Pharmaceutical Services, Inc.
Many biologic drugs, including cell and gene therapies, require low-temperature storage – under conditions that can range from refrigerated to cryogenic (< -150oC). But, such sub-ambient temperatures can be problematic for glass vials. If the glass vial for a biologic drug experiences breakage, or does not maintain container closure integrity (CCI), a cyclic olefin polymer (i.e., Daikyo Crystal Zenith® COP) system may be the solution. COP has several features, the combination of which is unique, that makes it suitable for drug packaging:
- very good resistance to oxygen and water
- fracture resistant
- lack of interactions with biologic drugs ability to maintain CCI at low temperatures
Before we dive into discussion of COP vials, let us review the issues with glass vials at low temperatures.
Challenges with Glass Vials
Glass has been used to store and deliver drugs for years — in vials, syringes, cartridges, and other containers. Glass is readily available, relatively inexpensive, and, in many cases, works very well. However, at the low-temperature storage required by advanced therapies, glass is prone to failure. Here’s why:
Breakage
Glass is intrinsically brittle. At low temperatures, it is even more brittle; thus glass vials are more likely to fracture. This is due in part to the residual stresses resultant from manufacture. Agitation from shipping/handling increases the likelihood of fracture, resulting in unusable product at delivery – an especially serious issue for a drug destined for a clinical trial, or worse, an autologous cell therapy.
Chemistry – Deleterious Interactions
Glass is not inert. It has a high-energy surface comprising functional groups (e.g., Si-OH) that can negatively interact with a drug product – especially biologics. In the case of biologics, resultant protein aggregation can potentially alter stability, purity or effectiveness. Clearly this is a risk to patient safety. Leachables (e.g., Na+) from glass pose the same risk. Another serious issue is delamination, the presence of glass flakes in drug product resulting from detachment of flakes from glass surface. Since 2010, this has caused many product recalls – FDA has issued a warning on this (https://www.fda.gov/Drugs/DrugSafety/ucm248490.htm).
Loss of CCI
At cryogenic temperatures, glass and rubber are fundamentally incompatible - resulting in a high likelihood of CCI failure of a (glass vial)-(rubber stopper) system. The reason is the substantially different coefficients of thermal expansion. See Table 1. Upon going from room temperature (~ 20oC) to cryogenic temperature (~ -180oC) – a change of ~ 200oC is encountered. A rubber component shrinks substantially more in volume than a glass component – 4.5% versus 0.2%. This difference can result in gaps between the rubber component and container, with concomitant risk of loss of CCI. In other words, rubber pulls away from glass at low temperatures. In contrast, rubber and COP shrink at comparable rates – 4.5% versus 4.1% – substantially reducing risk of gap formation and loss of CCI, as compared to glass.
Table 1. Coefficient Of Thermal Expansion (CTE)
|
CTE |
Volume Shrinkage (%) |
Glass | 4 | 0.2 |
Rubber | 77 | 4.5 |
COP | 70 | 4.1 |
Performance of COP
Work at West has demonstrated experimentally what was expected theoretically – the superior CCI performance of COP at cryogenic temperatures. Vial/stopper systems comprising COP and glass, were filled with air, and placed in the vapor phase of a liquid nitrogen chamber (approximately -165oC) for 8 days. The atmosphere was approximately 100% N2 gas at 1 atmosphere pressure. With frequency modulated spectroscopy, the O2 concentration in vials was measured. Results are shown in Table 2. Note the substantially better performance of the COP system – showing only a very slight change in O2 concentration. In contrast, the glass system showed substantial loss of oxygen. This is consistent with a leak resulting from the rubber stopper pulling away from glass vial. In the case of the COP system, note that good CCI was obtained even though rubber is well below glass transition temperature (ca. -70oC). There is a small loss of O2 in the COP system – likely resulting from a small amount of O2 and N2 exchange through COP vial walls. This might be expected, since it is well known that all glassy, amorphous polymers have some level of gas permeability. However, the key point remains, the substantially better performance of the COP system. Excellent performance at cryogenic temperatures would indicate excellent performance at other temperatures that a drug product might see: -120oC (air transport), -80oC (dry ice, ultra-cold freezer), -20oC (freezer). In fact, separate work at West has demonstrated the same good performance at -80°C.
Table 2. Vial Stopper Systems In Liquid Nitrogen
2 ml vial |
13 mm serum rubber stopper |
Total Samples |
O2 concentration (%) |
|
T= 0 days | T = 8 days | |||
Daikyo Crystal Zenith® COP | West 4432-50 Gray | 80 | 20.1 (σ = 0.11) | 19.4 (σ = 0.12) |
Daikyo D21-7S | ||||
Glass | West 4432-50 Gray | 80 | 20.4 (σ = 0.22) | 8.0 (σ = 0.11) |
Daikyo D21-7S |
The poor performance on the glass system presents an issue beyond possible damage to the drug from O2 exposure. With such a high leak rate, a substantial amount of N2 is moving into the vial - upon removal from liquid nitrogen, N2 contained within will result in an over-pressurization inside, which could result in stopper dislodging, or uncontrolled ejection of drug product upon piercing of stopper with syringe.
Conclusion
A system comprising a cyclic olefin polymer (i.e., Daikyo Crystal Zenith® COP) vial and a rubber stopper is an excellent choice for storage of biologic drugs. In addition to the many benefits of COP, which include lack of interaction with biologic drug, this system enables excellent CCI at cryogenic temperatures, whereas a system comprising a glass vial does not.
About the Author
Whitney Winters joined West in 2007 as a pricing specialist where she worked with a variety of start-up biotech companies and large pharmaceutical customers in order to identify testing opportunities and coordinate completion of projects to meet customer needs. In her current role as Senior Sales Director for emerging biologics, Whitney leads a team as they assist start up biotech companies in North American and Europe with containment and delivery solutions. Her team supports commercial opportunities, high value programs, pharmaceutical device systems, and custom product developments. She also helps to educate customers on the market trends for parenteral packaging as well as applicable guidance’s and FDA regulations.
Whitney received her MBA from Pennsylvania State University in 2011, and a B.A. with a specialization in chemistry from Northwestern University in 2002.
About West
West Pharmaceutical Services, Inc. is a leading manufacturer of packaging components and delivery systems for injectable drugs and healthcare products. Working by the side of its customers from concept to patient, West creates products that promote the efficiency, reliability and safety of the world’s pharmaceutical drug supply. West is headquartered in Exton, Pennsylvania, and supports its customers from locations in North and South America, Europe, Asia and Australia. West’s 2016 net sales of $1.5 billion reflect the daily use of approximately 112 million of its components and devices, which are designed to improve the delivery of healthcare to patients around the world.
Need More Information? Just Ask.
Click the button below to directly contact the supplier. Use it to:
- Ask a question.
- Request more detailed information or literature.
- Discuss your current project/application.
- Request a quote.
- Locate a distributor in your area.
- Schedule a demo.