Why You Need A Quality Culture — And How To Attain It
By Danielle DeLucy, ASA Training & Quality Consulting, LLC
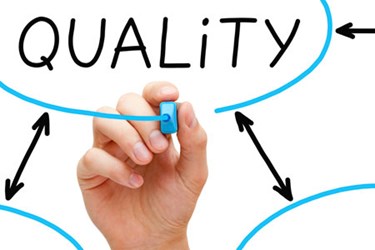
In today’s world of ever-increasing regulatory scrutiny on pharmaceutical quality we have all witnessed first-hand the public relations nightmare of adverse events, drug recalls, and even company closures. In response, pharma companies have set stricter rules and regulations for their employees to follow, to ensure they remain in compliance with regulators and avoid negative inspection results. This focus on quality — quality of the process, quality of the batch, quality of the final product, or even the quality of the whole operation — has led many manufacturers to seek establishment of a culture of quality among their employees.
But what exactly is a quality culture? In their seminal article Defining Quality, Lee Harvey and Diana Green outlined the nature of quality culture, which was seen at the time as a function of manufacturing industry: “A culture of quality is one in which everybody in the organization, not just the quality controllers, is responsible for quality.”1 As companies begin to develop their quality culture, the authors explained, they begin to adopt the philosophy if doing things right the first time. This type of behavior extends responsibility for quality beyond the quality group, out to the entire organization.
What are the benefits of quality culture? Organizations that foster development of a quality culture usually experience less employee frustration, less employee turnover, and more successful regulatory inspections. Working at such companies empowers employees on the shop floor level to become more engaged in improving the processes they perform every day, which improves motivation, company loyalty, and commitment to quality.
A successful quality culture does not happen overnight, however. It takes a commitment from upper management, mid-line managers, and shop floor employees to initiate and sustain such a movement and achieve its benefits. But what drives cultural quality as a necessary element in an organization? Is it a quality motto? A monetary award for employees that achieve zero mistakes? No. While each of these items are nice to have, establishing and retaining a solid culture of quality requires a few key steps.
First, you need to conduct a gap analysis to determine where the firm currently stands with regard to quality. A few questions to ask in this analysis are: What is the status of quality culture on the shop floor, in the warehouse, in the laboratory, and even in the office areas? Where does the organization envision itself in the future with regard to quality? What, in fact, are we trying to achieve? Setting goals for the organization helps build a strong foundation for a quality culture.
Getting answers to some of these initial questions can be relatively easy. For example, develop an employee survey to gauge where shop floor employees think process steps or environments need to be changed in order to improve quality. Hold regular employee/ upper management lunch chats provide face time with those responsible for making decisions. Have a contest to choose a quality motto. These are all great ways to begin developing a quality culture.
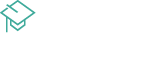
Let Danielle help you develop and implement a systematic, holistic quality risk management strategy in this webinar:
Applying Quality Risk Management (QRM) in Manufacturing – A Proactive Approach
Next, upper management must demonstrate its commitment to the mission of building a culture of quality. This will send the message to employees that quality is key to success at an organization. The leadership group should develop quality metrics for themselves and the staff, and link those metrics to their financial bonuses. Walking through the shop floor, talking with the employees, and getting a first-hand look at daily operations should take place on a weekly basis. This “walk the talk” type of initiative goes a long way with employees, as they begin to see that leadership is serious about quality. Data and suggestions gained from these walks should be acted upon if they involve improving processes, employee morale, or compliance in general.
Employee engagement is a technique that is very simple but powerful when creating a quality culture. Many managers and human resource departments think that employees are only motivated by raises and promotions. Although these can be great confidence boosters, they don’t always have lasting effect on engagement. Believe it or not, positive reinforcement for a job well done, asking employees for their own opinion on how something should be handled or improved, and rewarding teams with a dress-down day or a work-from-home day really resonates with shop floor employees. Non-monetary rewards can make employees feel valued and appreciated, which is an important step to sustaining a culture of quality.
Finally, ensuring that policies and procedures are in line with cGMP requirements is another important element to embedding quality in your culture. Procedures need to be easy to understand, yet detailed enough to make sure the process remains in compliance. Proper training of employees on these documents and processes is another key to success. Cut down the wordiness of documents to help the staff better understand the process, making them more efficient and ultimately more compliant.
Once you have all of these variables working together, the organization will start seeing a marked difference in the way their employees think about quality. This, in turn, will lead to a decrease in the number of deviations, lessening of process downtime, and a reduction in employee turnover — all signs that your efforts are working. Eventually, these initiatives will become less of a corporate “flavor of the day” and more of a way of life. This whole process will not require significant investments in time or resources, as the required elements are already present. However, it does take a group effort to make it successful.
References:
- Harvey, L., and Green, D., “Defining Quality”, Assessment & Evaluation in Higher Education, 1993.
About The Author:
Danielle DeLucy is owner of ASA Training and Consulting, LLC, which provides pharmaceutical- and biologics-based companies with training and quality systems assistance in order to meet regulatory compliance. Prior to this role, she spent 15 years in the industry serving in numerous quality management roles. She has helped lead many regulatory health inspections and was instrumental in the coaching process of her peers prior to any inspection. Currently, Danielle assists companies who are faced with warning letters or consent decrees, and those wishing to improve compliance, establish more robust quality systems.