Yugos & Dueseys: What "Classic" Cars Can Teach Us About Aging Facility Risks
By Christopher J. Smalley, compounding pharmacist advisor, ValSource
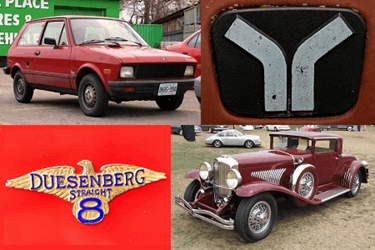
With an increasing number of pharmaceutical plants having been in service for decades, the topic of aging facilities has become a major concern for regulatory agencies. And rightfully so — aging facilities can contribute to quality issues and drug shortages, among other problems. But what exactly is an aging facility?
For instance, can we define an aging facility intuitively?
Using this method will tell us that an aging facility:
- Is not well-maintained
- Suffers from frequent deviations and/or batch rejections
- Is lagging behind compliance with current regulatory expectations
- Has outdated controls, process flows, and/or equipment, and
- Is older than [pick a number] years of age.
However, this last perception of aging facilities can cause the greatest confusion. A facility does not need to be old to be considered “aging.” Allow me to use automobiles to illustrate this dilemma.
Is Your Facility A Yugo Or A Duesey?
In 1985, a car called the Yugo was introduced to the U.S. market from Yugoslavia. It sold for $3,990 and listed carpeting and rear window defrosting among its few features. The car quickly developed a reputation for poor drivability and quality, leading Time magazine to include the Yugo on its list of The 50 Worst Cars of All Time (and to speculate that the rear window defroster was included to keep your hands warm while pushing the car). This is a prime example of age being an unreliable indicator of equipment, facility, or a system performance.
Deterioration of systems can also depend on preventive maintenance (PM), and increasingly on predictive maintenance (PdM). In fact, PdM is becoming the new pharmaceutical industry standard, relying less on the passage of time than on real-time data about how the component or system is performing.
Another consideration that does not relate to age is the robustness of the process. Is the manufacturer using processes that were not robust to begin with? Perhaps the processes were accepted in order to achieve the best possible launch date, but now those processes are contributing to the attributes that characterize an aging facility.
Or maybe the facility design is not compatible with current process and/or personnel flows, due to changes in product and isolated upgrades — these certainly take place over the course of time, but they are not directly related to age. For instance, the addition of gowning rooms or airlocks can convolute the original design of product/process flows and personnel flows.
Yet another age-agnostic example (that might resonate with many operating facilities) is when regulatory expectations change based on a crisis identified at another company’s facility. All of a sudden, a new requirement is imposed that your facility was not designed to accommodate. Or, basic utilities such as water and HVAC can become strained by the additional demands from a well-intentioned CAPA.
Revisiting the automobile analogy, let’s look at another perspective. From 1928 through 1930, the Model J was produced by Duesenberg Motors Company, out of St. Paul, Minnesota. It was simultaneously an outstanding luxury car (built entirely by hand to the owner’s specifications) and outstanding performance car (the fastest on the market at the time). It is thought to be the source of the expression, “It’s a Duesey!”, meaning something is the finest of its kind. Considering the Model J was produced more than 85 years ago, some might consider an existing the Model J to be an “aging car,” but with the proper maintenance and upkeep, it can continue to be an outstanding performance and luxury automobile to this day.
So how does this relate to defining an aging facility based on intuition? Unfortunately, intuition is many times driven by perception and emotion, not by science — and so is a poor gauge of condition and quality.
Quality Risk Management: A Scientific Way To Evaluate Aging Facilities
Quality risk management (QRM) is the best way to reduce subjectivity around evaluation of aging pharmaceutical facilities, helping you identify, assess, and control facility risk in a dispassionate manner.
QRM provides the means to understand the potential hazards / failure modes associated with the existing process, systems, and equipment that are part of what might be perceived to be an aging facility. The goal is to identify these hazards and prevent them from materializing by adding controls that not only modernize the facility, but also keep an aging one working as intended.
The first step is to ensure that the right risk question is being asked. The risk question is the basis for QRM and serves to focus the effort, no matter what risk tool is selected (more on that in a moment). The question can apply to building systems that are susceptible to performance deterioration, such as HVAC systems whose ductwork may begin to leak, for example, or architectural features that pose contamination challenges, such as painted walls that can flake or harbor dust and dirt. The question should also take into account current regulatory requirements and expectations, and trends in deviations and out-of-specification incidents. It needs to be specific to each facility and application, so there are no “cookie cutter” risk questions. As an example, a risk question might be, “What issues are contributing to batch rejections occurring during the purification process?”
The second step is to select of SMEs to participate in the risk assessment. In many organizations it is common to select managers or directors. For aging facilities, however, it is crucial that manufacturing operators, mechanics, quality technicians, deviation investigators — the people who are engaged with the process, systems, and equipment intimately, on a daily basis — are part of the team. Their knowledge of the nuances that are not captured in any data stream is crucial to the success of the risk assessment process.
With the right risk question and the right SMEs engaged, the next step is to choose the most appropriate tool for performing the risk assessment, to determine if indeed it is an aging facility. Failure mode and effects analysis (FMEA) may offer the best benefits when evaluating an existing facility. Your organization may use other tools, and certainly there is an advantage to using a tool that your team and facilitators have been trained in, but FMEA leverages the experience that only the operators, mechanics, and technicians possess.
It is also important to ensure that management makes the SMEs identified available to participate fully in the risk assessment meetings — and that all data is made available. As an industry, we accumulate mountains of data, but frequently the data is not shared far beyond a specific department or two. We must make data available for sharing in a systemic way, but knowledge management is a topic to tackle in a different article.
Once the risk assessment has been conducted, management can now understand, dispassionately, if there are signs and symptoms of an aging facility, but the work doesn’t end there. Don’t allow the risk assessment to be filed away. The risks that have been identified need to be controlled. Take action on those risks that have been prioritized in the risk assessment.
You may not be able to eliminate all risks, and it is important to communicate those to management — and obtain understanding of the risks and the impact of their acceptance. This is where risk communication comes in. Risk communication is also used to address the obstacles that need to be addressed in implementing risk control. Is risk control just a matter of resources (people and dollars), or does it entail issues such as managing the risk of supplying product to the patients? Do you build inventory or do you implement the changes in an operating facility?
The next stage in the QRM process is risk review, when the team reviews the risk controls after they have been implemented. The review is intended to check the effectiveness of those controls, because if they are not working, the risk assessment will need to be revised to determine the residual risk. How many times have you encountered a corrective action plan that inadvertently creates a new problem (which is also a new risk)? How many times have you implemented a corrective action plan with the best of intentions, but it doesn’t completely address the risk?
One Size Does Not Fit All
The signs of an aging facility can manifest themselves in a myriad of ways, and there is no cookie cutter approach that I can offer to identify them. However, trying to evaluate an aging facility intuitively will only result in an ineffective and superficial result. Taking a scientific approach that engages those who have the knowledge of the facility — from working with it daily — will yield the most accurate aging facility risks.
This article is based on a presentation made by the author at a PDA Delaware Valley Chapter meeting in September 2016.
About The Author:
Chris Smalley recently retired from Merck, where he had responsibility for innovative implementation and validation, including single-use systems, globally. Previously, he was director of quality operations for Wyeth Pharmaceuticals for 12 years, with responsibility for setting validation standards and validation activities globally. His research experience includes responsibility for quality in the U.S. operations of the Sanofi Research Division, and earlier he worked for the Johnson & Johnson family of companies, where he was a plant manager. Chris is a graduate of the Philadelphia College of Pharmacy of the University of the Sciences in Philadelphia. His graduate education includes an MBA from Temple University’s Fox School of Business and an MS in pharmaceutical chemistry from Temple University School of Pharmacy.
Chris has been a member of the PDA Board of Directors, as well as a member of the PDA Science Advisory Board. Currently he is a member of the ISPE Disposables Community of Practice (COP). You can reach him at Chris.j.smalley@gmail.com or on LinkedIn.
Image credits (clockwise from top left): Red Yugo GV in Junction Triangle, Toronto, Canada 2 (Michael Gil, 2011, CC BY 2.0), Yugo badge on a red Yugo GVL (Y, 2010, CC BY 2.0), Duesenberg J Judkins 1932 (Ramgeis, 2004, CC BY-SA 3.0), Duesenberg logo (Jim Culp, 2012, CC BY-NC-ND 2.0)