Syntegon Pharma Technology Inc.
Jerry Jean-Baptiste
8700 Wyoming Ave N,Minneapolis, 55445
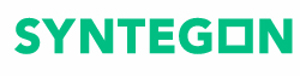
Company Overview
Syntegon is one of the leading providers of process technology and packaging solutions for the pharmaceutical industry. Our portfolio includes single units, systems and complete solutions for all process steps and packaging types. Discover our packaging solutions for pharma, biopharma and fine chemicals.