Optimize Scale-Up And Increase Capacity For Vaccine And Therapeutic Manufacturing
By Robert Hendrix, Staff Engineer, Systems Design, Single-Use Technologies; Kathryn Barnes, Process Improvement Manager, Production Chemicals and Services; Joe Gallo, Associate Product Manager, Production Chemicals and Services; Julie Bray, Production Support Services Senior Manager, Pharma Services; Adam Goldstein, Sr. Director, Research and Development Collaborations, Single-Use Technologies; Thermo Fisher Scientific
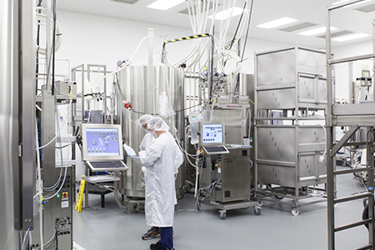
Accelerate development and manufacturing in the era of SARS-CoV-2
To meet the urgent demand for SARS-CoV-2 vaccines and therapeutics in the shortest possible timeframe, many companies are designing their scale-up processes in parallel with Phase III clinical trials, redefining the risk tolerance for everyone involved. To satisfy commercial requirements for expedited scale-up, the molecule can no longer dictate the technology transfer process into the manufacturing facility.
Shifting the focus from optimizing an individual process to an entire biomanufacturing workflow requires companies to adopt a new mindset and consider new ways of doing business. Success can be achieved by concentrating on three key activities: reviewing capabilities, assessing your risk tolerance, and identifying additional resources to accomplish your goals.
Rethink Your Current Capabilities
It’s important to determine if you have in-house manufacturing capabilities that can scale to compete in an accelerated race with other developers and manufacturers for first-to-market vaccines and treatments. Critical process optimization considerations include equipment, capacity, chemicals, consumables, a skilled workforce, and supply chain flexibility with redundancy. Consider these questions:
Has your organization committed to the development of robust time-and-motion modeling approaches at scale to drive decisions?
At scale, time-and-motion models are incredibly powerful tools when correctly integrated into an organization. These models become the foundation of all engineering and resource-specific questions when predicting if the current capabilities of an organization can scale to meet the challenges of a novel project. To understand the significance of these models, consider how much time it takes from the start of equipment setup to the end of equipment breakdown. Organizations without significant experience developing time-and-motion models are well advised to seek a partner with that expertise to bridge the gap between current capabilities and future requirements.
Could product standardization help to better meet demand?
Product standardization has advantages. For example, selecting single-use bioprocess containers with consistent materials and components makes it easier to achieve consistent results. There is less variety in the materials of construction, which reduces the number of validations or in the case of a new material of construction—revalidation— necessary. Standardization also ensures that the same components are used throughout the process. Therefore parts are more likely to be in stock from both the vendor and the sub-supplier to the primary vendor, and internal training at the site is minimized because fewer diverse components are in use.
How will you share data and maintain data integrity?
Ideally, one automation and control platform would be used from R&D through manufacturing. Not only would selecting one platform help ensure data integrity, but it would also help to mitigate capital expense and operational costs. The more additional equipment that needs to be purchased, the more likely it is that you’ll need to invest in facility upgrades, personnel skills and training, and chemical formats, making supply chain adjustments necessary.
Will your current head count be able to support the increase in demand?
Outsourcing workflows that include process liquid and buffer preparation can enable you to focus your work force on optimizing other processes. Receiving process liquids and buffers as they are needed for production eliminates the need to precisely weigh, dispense, and hydrate dry chemicals. The time spent setting up, working in, breaking down, and cleaning up work areas for bioprocessing steps tends to be underestimated.
Staff need to be specially trained for each of these steps, with additional trainings required for handling hazardous materials. Letting experienced professionals handle noncore activities like those described above, will save time, money, and storage space in the long run.
Have you considered secondary sourcing and stocking agreements to improve on-time-in-full (OTIF) performance?
Secondary sourcing is a key safeguard for mitigating production delays. Suppliers with global manufacturing capabilities and networks can enable you to specify raw materials from alternate suppliers into your processes. If the primary supplier runs into unforeseen supply chain issues, such as material unavailability or long lead times, you have ready access to raw materials from back-up suppliers. Stocking agreements are another safeguard to ensure raw materials are delivered on time, and in the order’s entirety. Having the right raw materials available for use at the right time is key to ensuring production schedules can be met as well as optimizing facility capacity.
Assess your levels of risk tolerance
Once you have assessed your current capabilities, consider what risk levels your company can tolerate from development to commercial manufacturing.
When making development decisions, are you considering the impact on commercial manufacturing?
Due to the speed at which the industry is moving to produce vaccines and therapeutics for SARS-CoV-2, it is critical to keep cGMP manufacturing in the forefront of the development process. Doing so will ensure that regulatory requirements can be met without significant delays. Starting with the end goal in mind while in development will help mitigate risks when commercialization is reached—in many cases, development and manufacturing are occurring in parallel.
Have you considered making your supplier a true partner to reduce risk?
Outsourcing noncritical tasks to a highly qualified partner not only enables you to focus on core activities, it also takes much of the burden of meeting manufacturing schedules off your organization and places it on a partner who is experienced with minimizing downtime. This allows you to better utilize your internal resources, both people and equipment, in a more valuable manner. Production delays can occur for many different reasons.
Two of the most common reasons are operator/ engineering design errors and supply chain issues. Operator/design errors can, and do, occur at many different scale-up steps, resulting in production delays and even product losses or failure. Whether from lack of training, rushing, or distractions, chemicals or consumables may be mishandled, misformulations may be made, chromatography columns may be improperly packed and cleaned, etc. The result of these mistakes may be environment, health, and safety issues, the need to rerun process steps, and regulatory approval delays. Outsourcing process steps to bioprocessing experts can minimize some of these costly mistakes.
The increased demand for manufacturing is creating unanticipated constraints in chemical supplies, increasing the possibility of delays in product deliveries and in meeting manufacturing deadlines. Supply chain issues can be minimized with a global partner who secures secondary and/or dual sourcing early in the process to ensure chemicals, components, and products meet manufacturing specifications, and will be available as needed. These are important steps to maintain business continuity and minimize downtime.
Where to find additional help and support
Robust collaboration throughout the entire biomanufacturing process is key to implementing an optimized scale-up process. Consider which new changes to the process would be acceptable, even advantageous, and which would incur lengthy delays or derail the project. While some companies may have the internal structure and talent needed to collaborate effectively, it’s always a good idea to benchmark with experts in the areas of biomanufacturing, including logistics, and qualification services, to better identify possible stumbling blocks. Lean manufacturing practices, like routinely conducting Gemba walks, are central to helping identify waste or areas of concern that could lead to failures, which equates to accelerating scale-up. These practices can—and should— be implemented with the support of a capable partner who will bring new perspectives and ideas to elevate your existing workflows.
Due to the unique challenges to global supply chains caused by SARS-CoV-2, companies are advised to assess their current supplier relationships and create partnerships where gaps have been identified. Rather than managing multiple vendors, companies can significantly benefit from choosing an experienced partner who can collaborate, consult, and support the implementation of solutions throughout the full range of biomanufacturing workflows. A strong partner candidate will have a robust network and a capable pool of experts to consult on process optimization, scale-up, manufacturing, and validation support as required.
Looking forward
As we look toward the future, therapeutic and vaccine development is likely to continue to accelerate. Companies should review the following critical actions to optimize vaccine and therapeutic manufacturing and remain competitive.
- Assess your current capabilities and consider partnering with experts in time-and-motion development models to ensure you can bridge the gap between current capabilities and future needs
- Review your tolerance for risk to make sure you have considered potential bottlenecks that can be avoided through investments in partnerships and outsourcing
- Consider outsourcing any noncore manufacturing processes to accelerate scale-up timelines and to increase your ultimate capacity
- Plan for secondary and dual sourcing early to minimize supply chain disruptions that could cause production and commercialization delays
In any case, organizations must develop flexible mindsets and consider partnerships to optimize scale-up processes.