Single Use In Biopharma: Beyond Savings & Sustainability

By Matthew Pillar, Editor, Bioprocess Online
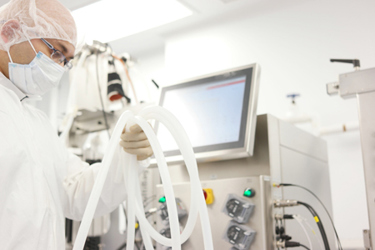
Single-use technologies (SUTs) continue to trend in biopharmaceutical applications, driven largely by environmental and economic considerations. But there’s a lot more to the SUT story—supply chain and standardization advantages, for instance—so we dove deep with independent SUT expert Paul Priebe and Krystal Biotech VP of Technical Operations Mark Petrich. Dial up the full 60-minute discussion on-demand here. In the meantime, here’s some fodder we addressed during the conversation.
Despite Disposal, SUT Is Greener Than Stainless
Everyone knows that traditional stainless steel-based manufacturing processes require extensive cleaning and sterilization procedures between batches, resulting in substantial water and energy consumption. SUTs, on the other hand, virtually eliminate the need for such rigorous cleaning protocols. Studies conducted by BioPlan Associates and BIO (Biotechnology Innovation Organization) consistently demonstrate that SUTs can reduce water usage by up to 70% and energy consumption by up to 50% per batch compared to conventional methods. The SUT supply chain is also purported to reduce carbon emissions – SUTs are generally lightweight, and their compact design lends to efficient transportation. Why haul one bioreactor when you can haul a dozen at lower cost? While concerns about the environmental impact of disposable plastics are valid, there’s much work being done on that front, in terms of both responsible disposal and safe recycling practices.
It Costs A Lot To Fail. Why Fail In Stainless?
Most folks also know that biopharma manufacturing traditionally requires an investment of several hundred million dollars in capital equipment, much of that investment comprised of stainless steel. While the initial investment required of SUTs isn’t trivial in comparison, it pays back in the long run. According to the Journal of Biotechnology and Bioengineering, the total cost of SUT ownership over a five-year period can be up to 25% lower than that of traditional stainless steel setups. This reduction in costs is primarily attributed to the elimination of expensive cleaning and validation procedures, as well as the increased flexibility and scalability that enables more efficient resource utilization and reduced downtime. The modular nature of SUTs enables easier adaptation to evolving production needs, mitigating the risk of overinvestment or underutilization of manufacturing capacity.
In a business that regularly requires a decade of manufacturing activity to create the slightest chance of product approval, a 25% savings at the five year mark can have big impacts on corporate longevity.
Meeting Standards Out Of The Box
SUT standards have matured, to the point that single use adoption no longer threatens regulatory efficiency. Standards such as those established by organizations like the International Organization for Standardization (ISO), ASTM International, Bio-Process Systems Alliance, the American Society of Mechanical Engineers Bioprocessing Equipment Subcommittee, the BioPhorum Operations Group (BPOG) and others provide guidelines and best practices for the design, implementation, and validation of SUT. Adhering to these standards ensures consistency, reliability, and compliance with regulatory requirements, such as Good Manufacturing Practices (GMP) and Current Good Manufacturing Practice (cGMP) regulations. By providing a framework for quality assurance, these evolving SUT standards help mitigate risks associated with product quality, safety, and efficacy, ultimately facilitating smoother regulatory approvals.
SUT standards also outline protocols and methodologies for conducting comprehensive validation studies, including extractables and leachables testing, integrity testing, and biocompatibility assessments. With clear guidelines for validation protocols and documentation requirements, these standards can help manufacturers streamline the validation process, reduce redundancy, and ensure consistency in data generation and reporting. Through their involvement with ASME and BSPE, Paul and Mark are both actively involved in standards consideration and have a lot to share about self-governance and industry involvement.
Establishing A Single Use Supply Chain
The supply chain snafus we saw during COVID taught us that effective supply chain management is critical for ensuring the availability, traceability, and quality of single-use components. Standards related to material selection, manufacturing processes, packaging, and labeling help establish criteria for assessing supplier qualifications, evaluating product quality, and managing inventory effectively. By adhering to these standards, manufacturers can minimize the risk of supply chain disruptions, ensure product traceability, and maintain the integrity of single-use systems from procurement to disposal.
With this proliferation of SUT from a long (and growing) list of manufacturers, ensuring interoperability and compatibility among products has become critical, especially in multi-sourced manufacturing environments. Standards play a pivotal role in establishing common specifications and requirements for connectors, tubing, bags, filters, and other components, enabling interchangeability across different platforms. This interoperability fosters flexibility in process design and equipment selection, allowing manufacturers to adapt to changing production needs more efficiently, and increasingly, without concern for regulatory review.
As the biopharmaceutical industry evolves, single-use technologies are evolving with it. They’re more sustainable, more standardized, and in greater supply than ever. Explore the virtues of single use and evaluate its adoption, or expansion, in your bioprocessing environment. Watch the conversation with Mark and Paul on demand here, compliments of Colder Products Company and Entegris.