The Advantages Of Blow/Fill/Seal Processing For Vaccine Production
By Marty Reyes
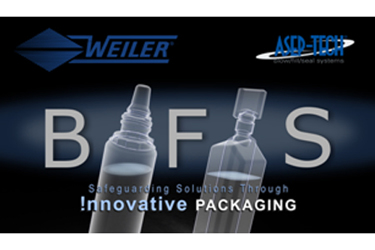
Traditional vaccine production often includes an equally traditional vessel for end products: multi-dose glass vials, which have served as the standard for many drugs for decades. However, the use of glass vials creates a number of challenges for manufacturers and providers alike, which has led to recognition among regulators that advanced aseptic processing techniques, like blow/fill/seal (BFS), offer greater safety and customization for drug product manufacturing.
Multicomponent filling and sterilizing systems represent unique advantages for vaccine production. Discover how these systems can be adapted for vaccine production without incurring any product degradation, and their widespread implementation can be achieved through adaptive strategies centered on experience, scientific principles, and long-term, global strategies.
Get unlimited access to:
Enter your credentials below to log in. Not yet a member of Pharmaceutical Online? Subscribe today.