The Importance Of Container Closure Integrity (CCI) Feasibility Testing
By Brian Svaton
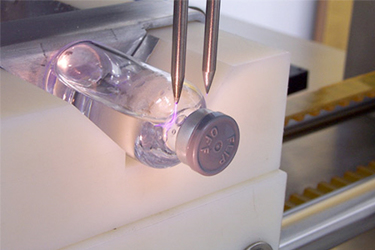
Container Closure Integrity Testing (CCIT) in the pharmaceutical industry is such an important piece of the packaging puzzle, that more and more regulatory agencies around the globe are beginning to draft specific requirements for manufacturers. With the greater need to meet these requirements, product inspection companies are evolving their technology to meet the increased speed and efficiency demands of the packaging lines. An absolute truth in the CCIT space is that one single inspection technology cannot be used for every type of pharmaceutical product.
Therefore, you should always weigh the various factors to determine the ideal inspection methodology. These factors include but are not limited to, solid vs. liquid form, type of container (glass, plastic, etc.), fill volume, viscosity, conductivity, production speed, and temperature or oxygen-sensitive products including vaccines, biologicals, or anything albumin-based. So how does one determine the best inspection method for their particular product? Feasibility testing!
THE TESTING PROCESS
Feasibility testing provides the information necessary to help steer manufacturers in the right direction when it comes to CCIT. Nikka Densok USA, for example, offers complimentary feasibility and exposure testing with their full suite of HVLD* (High Voltage Leak Detection) equipment. The goal, for Nikka Densok, is to provide a high-speed production solution to its customers by opening the door via free product testing. Brian Svaton, the technical manager at NDUSA mentions, “We typically sign a quick NDA with the customer and request samples, which are then shipped directly to our testing facility in Golden, CO. There we have testing equipment for different types of liquid-filled containers, including glass vials, ampoules, syringes, IV bags, and BFS bottles or cards. The expectation is that we determine whether HVLD is the right fit for a customer’s product and hopefully provide them with a long-term solution.”
CREATING DEFECTS
One key challenge when performing feasibility tests on different types of containers is how to create measurable and repeatable defects. In addition, many customers request to test “real-world” scenarios that are often hard to re-create, including cracks in glass vials or defective liquid stoppers. These challenges are overcome using both creative methods and also very precise techniques such as drilling laser holes (see below for more info). Stopper or plunger defects in syringes and vials can be created using micro-tubing with specific diameters. Critical cracks in glass, which are more likely to happen during the manufacturing process than many other issues, can also be created using different tools but are less repeatable and a bit more subjective. One much-debated question is, “How do you measure a crack?” The key takeaway is not necessarily measuring the crack, but instead acknowledging that a crack is indeed a critical defect and can cause a catastrophic leak in glass.
Laser drills can create much smaller and repeatable holes in glass and plastic, often as small as 5 microns or less. Prior to testing, samples must be sent to a laser drilling company (such as Lennox Laser) which can add weeks to the process. While this process is often the best way to challenge different CCIT technologies with such small holes, the additional time requirements make it prohibitive. If time is of the essence, Nikka Densok, for example, can use acupuncture needles onsite to create defect holes as small as 100 microns in BFS plastics and IV bags.
THE DATA
The results of these tests include full reporting on the technology’s detection capabilities and often include graphs, pictures, and even video of the inspections being performed. Test results often can be completed in less than 48 hours. Used samples are either shipped back to the customer or destroyed. With this data in hand, scientists, product managers, production engineers, and other stakeholders can make educated, data-driven decisions on what CCIT is ideal for their situation.
With the global demand for vaccines and especially faster production schedules, the need for integral product containers is greater than ever. Whether it’s a liquid, lyophilized, or solid-dose product, the need for increased CCIT will continue in the pharmaceutical manufacturing world, and feasibility tests will play an even more critical role in the near future. Ideally, with the right data in hand, manufacturers can make educated and data-driven decisions that will lead to ensuring a sealed, defect-free quality product is delivered to the public.
*HVLD Technology is a recommended method for parenteral liquid package inspection as Listed in USP Chapter <1207>. In determining whether Nikka’s HVLD system is the right fit for your product, we build data that can be scaled into our production equipment which in turn saves the customer time and money.