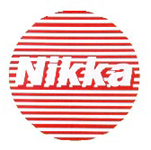
ABOUT NIKKA DENSOK USA, INC.
For more than 30 years, Nikka Densok Ltd. has been a global provider of Leak Detection Equipment designed for a variety of pharmaceutical packaging ranging from laboratory use to fully integrated production applications.
CONTACT INFORMATION
Nikka Densok USA, Inc.
700 Corporate Circle, Suite H
Golden, CO 80401
UNITED STATES
Phone: 303-202-6190
Contact: Brian Svaton, President
FEATURED ARTICLES
-
Advanced IV bag inspection technologies ensure patient safety and regulatory compliance in drug manufacturing. Learn more about automated leak detection and quality control innovations to optimize your business.
-
Medical and pharmaceutical products are often packaged in fluid-filled containers. Learn about CCIT using high voltage leak detection (HVLD), how HVLD technology works, and more.
-
A majority of methods used to detect pinholes, cracks, and defective seals in containers are destructive. Learn about High Voltage Leak Detection (HVLD) and why it is free from these shortcomings.
-
In the event of an IV bag leak, contaminants can adversely affect the solutions within. Learn how the reference standard for CCIT, USP 1207, applies to the CCIT inspection method of IV bags.
-
In the CCIT space, one single inspection technology cannot be used for every type of pharmaceutical product. You should always weigh the various factors to determine the ideal inspection methodology.
-
Learn in detail about High Voltage Leak Detection (HVLD), packaging applications that can be inspected with HVLD, and how to determine the best leak-testing method for your application.
-
Here, two of the more common methods for container closure integrity testing, high voltage leak detection (HVLD) and vacuum decay, are compared.
BROCHURES
- High Voltage Leak Detection Systems For Syringes
- High Voltage Leak Detection Systems For BFS Vial Cards
- High Voltage Leak Detection Systems For Glass Vials
- High Voltage Leak Detection Systems For Small Bottles
- High Voltage Leak Detection Systems For Glass And BFS Vials
- Pinhole Inspector For IV Bags And Flexible Packaging
- HDK Pinhole Inspector For IV Bags
- HDV-AT6 Pinhole Inspector For Glass Vials
- HDV-AT3 Pinhole Inspector For BFS Small Bottles
- HDC-4 Pinhole Inspector For BFS Large Bottles
- HDI Pinhole Inspector For BFS Vial Cards
- HDT-2 Pinhole Inspector For Sampling And Inspection Of Glass And BFS Vials
- Pinhole Inspector For Sampling And Inspection Of Glass And BFS Vials
- HDB-II Pinhole Inspector For Glass Vials & Ampoules