The 4 Phases Of CAPA Maturity: A Guide To Mastering Quality Event Management
By James Jardine
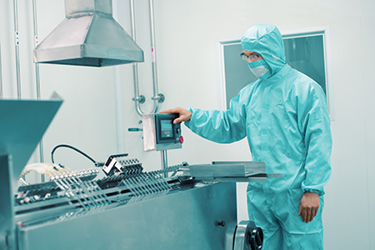
Even more important than being a regulatory requirement, an effective CAPA process should have a direct and measurable impact on improving product quality. An effective corrective action process accounts for all the potential sources of a quality issue and provides a feedback mechanism to prevent it from recurring. An effective preventive action process minimizes the number of quality deviations that occur in the first place. Taken together these two processes should reduce product returns, recalls, scrap, and warranty claims.
The CAPA tools and procedures used in quality event management processes are the primary factors that determine the success or failure of the overarching QMS. Most companies follow an evolutionary path in developing the correct set of procedures and tools required to maintain an effective CAPA system. Companies doing business in regulatory environments often start with a paper-based system because it offers familiarity and a seemingly low start-up cost. Next, it’s common for a company to move to a hybrid paper/electronic system with the aim of making their paper-based system more efficient. The next step is to either create a custom application that is completely digital or purchase commercially available, purpose-built CAPA management software. The following is an examination of the common pitfalls and potential benefits of each type of solution.
Get unlimited access to:
Enter your credentials below to log in. Not yet a member of Pharmaceutical Online? Subscribe today.