4 Trends In Recent FDA Warning Letters To OTC Drugmakers — And How To Avoid Them
By Alan D. Greathouse, The FDA Group, LLC
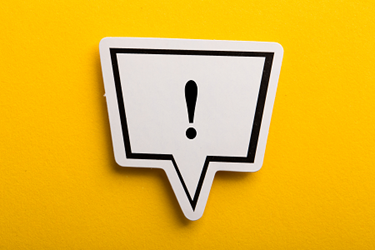
A recent flurry of warning letters issued to manufacturers of over-the-counter (OTC) drug and health products has revealed similar deficiencies related to current good manufacturing practice (GMP) and quality management expectations.
Many of the fundamental issues that appear repeatedly in these warning letters indicate underlying inadequacies within the quality management system (QMS). These include microbiological contamination control and detection due to poorly managed controls and a lack of suitable and validated testing, flaws in manufacturing operations and quality assurance, poor nonconformance management, and issues related to the establishment, responsibilities, and authority of organizational departments — namely the quality unit (QU).
While suggesting these issues are to some degree widespread among makers of certain products requires a speculative jump, it’s likely that these themes are present in the minds of inspectors and therefore may serve as a general roadmap for prioritizing internal QMS audits and any necessary remediation efforts accordingly.
A previously reported analysis of recently issued GMP warning letters characterized manufacturers of OTC nonprescription drugs as “the breakaway category” of firms issued warning letters throughout FY2018, receiving over half of all warning letters in the broader drug space.
This trend data, plus FDA news releases published in April and May that call specific attention to manufacturing quality issues potentially affecting patient safety among makers of homeopathic products, should prompt similar firms to evaluate their own quality systems for the four common patterns of noncompliance summarized below.
1. Documented Adherence To Relevant Regulations And Standards
Many recent warning letters highlight fundamental issues related to the understanding and practical implementation of the 21 CFR 200 series, as well as relevant USP standards that address specific types of products and the systems used to produce them.
Because the rules in the entire 21 CFR 200 series explicitly address handling, storage, labeling, processing, donor selection and a host of other relevant elements, they impact both manufacturers and the firms they partner with to produce and market products, including suppliers and contract manufacturers.
As a starting point for prioritizing self-assessment in the context of these recent citations, OTC drug and health product manufacturers should take it upon themselves to assess their functional understanding and adherence to 21 CFR 200 series regulations and make any necessary improvements as a proactive compliance initiative.
2. Establishment And Suitability Of Analytical And Microbial Testing And Validation Methods
Inadequate method development (method suitability and validation in particular) is another common theme in recent warning letters issued to OTC drug manufacturers. These critical processes are complex, often involving wide specifications, broad parameters, and the inherent variation that comes from working with living organisms.
Regulatory bodies like the FDA expect manufacturers to develop and thoroughly document testing methodologies that effectively neutralize any antimicrobial effect and allow control organisms to grow in expected numbers.
Conducting these activities properly requires strict adherence to criteria set out in USP guideline. It is absolutely critical to have the appropriate comparison controls in place to ensure method development is properly carried out and the optimal technique is used.
When considering questions for guiding self-assessment efforts, the following areas may be helpful starting points:
- Compliance with relevant USP (and other) standards for product testing
- Compliance of sampling handling procedures
- Outsourced sample testing
- Appropriate labeling and shipping of testing samples
- Ability to demonstrate integrity of shipped samples
- Method suitability to ensure testing methods are appropriate and effective to particular microbiological organisms
3. Nonconformance Management
Another recent trend afflicting OTC drugmakers mirrors a broader and well-documented trend throughout the drug and device space: inadequate nonconformance management. As demonstrated by the large number of citations issued specifically for “inadequate, incomplete, and undocumented investigations,” these warning letters offer evidence of a long-standing perception that an outsized focus is placed on immediate nonconformance correction rather than on thoroughly investigating and executing corrective and preventive actions following a comprehensive root cause analysis.
To reiterate what’s become a topic of particular focus given this problem’s stickiness, regulators expect firms to understand and use nonconformance management as a vehicle for improving processes and procedures that eliminate nonconformances based on the results of root cause investigations. While there are many valid perspectives on what makes for an effective system, few would disagree that one of the most critical points is the initial investigation into the nonconformance to determine the root cause. To conduct a thorough root cause analysis that meets the expectations of regulators, teams must be qualified to use proven analysis tools that enable them to examine the impact of process inputs and their effect on the nonconformance.
4. Roles, Responsibilities, And Authority Of The Quality Unit
The internal quality unit (QU) has been the target of many recent warning letters to OTC drug and health product manufacturers as an underlying cause of product quality and GMP compliance problems.
Numerous firms have been cited for having an inadequate QU. In the most egregious examples, firms lacked this designated team entirely. More often, however, regulators have cited firms for a lack of written procedures that govern the responsibilities and functions of this group. 21 CFR Part 211 is clear about the need to establish a “quality control unit” with the documented responsibility and authority to make critical decisions.
More specifically, FDA regulations and guidance documents reveal a number of general and specific duties expected from the QU. These include the establishment, management, and routine auditing of the quality system; the establishment of procedures, specifications, and proper manufacturing controls; nonconformance investigations; and management reporting, just to name a few.
In addition to its establishment, the QU should also be properly staffed and managed to reliably carry out the functions it’s required to perform. This group also must have access to the data it needs to make informed decisions regarding product quality.
Conclusion
Based on an increasing number of relevant warning letters, as well as analyses of enforcement trend data and public statements made by the FDA, it’s clear that a renewed focus has been placed on evaluating manufacturers of OTC drug and health products in key areas of GMP. These areas of enforcement focus include ineffective quality units, poor testing of incoming materials and components (i.e., relying on a supplier’s certificate of analysis), poor product testing, poor analytical and microbial testing and validation methodology (including method suitability), and inadequate nonconformance management.
In response, OTC drug and health product manufacturers should carefully assess their own state of GMP compliance with special attention given to priority areas and perform the necessary remediation efforts to bring their organization into full compliance.
About the Author:
Alan D. Greathouse has over 15 years of GMP manufacturing experience focused on parenteral drug products. Throughout his career, he has focused on manufacturing processes optimization and identifying and correcting operational inefficiencies. He has experience in life science production supervision and has served as a lyophilization expert and principal pharmaceutical consultant. He currently oversees consulting and contract staffing operations as senior director of quality and service assurance at The FDA Group. Access his downloadable guide and checklist covering these and other GMP and QMS assessment suggestions here. He can be contacted via the online contact form at thefdagroup.com.