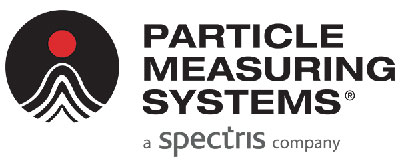
ABOUT PARTICLE MEASURING SYSTEMS
Particle Measuring Systems (PMS) provides Pharmaceutical aseptic and controlled manufacturing customers with the superior knowledge, technology, quality, and service you need to successfully meet global regulatory requirements and manufacture your product to the highest quality possible. Partnering with our customers, we provide a complete contamination monitoring solution. Starting with our Advisory Services team to assess risk, then collecting data with our world-class viable and non viable particle counters, through to compliant data management, analysis and reporting. We have the expertise to help you meet global regulatory requirements and get your product to market. As one of the world’s leading clean room contamination control experts and complete solutions provider, we offer fully integrated and robust monitoring solutions including:
- Particle Counters and Microbial Samplers, portable/mobile and remote/continuous
- Environmental and Facility Monitoring Systems (FMS)
- Data collection and fully compliant data management
Additionally, we offer a wide variety of expert Advisory Services including:
- Sampling locations
- Risk Assessments – avoiding 483’s
- Thermal Validations
- Crisis Handling – 483 management and response
Founded over 50 years ago, PMS is a trusted thought-leader in the Pharmaceutical clean manufacturing and other Life Science industries. Our team provides multiple webinars, papers, and training throughout the year to support professionals and cleanroom manufacturers with reliable guidance on the application of and compliance to global regulations.
CONTACT INFORMATION
Particle Measuring Systems
5475 Airport Blvd.
Boulder, CO 80301
UNITED STATES
Phone: 303-443-7100
Contact: Nina Morton
FEATURED ARTICLES
-
Learn how EU GMP Annex 1 (2022) redefines cleanroom air monitoring standards and emphasizes continuous viable sampling in Grade A and B environments to ensure aseptic integrity and compliance.
-
Discover the five essential principles of cleanroom particle counting and how they ensure compliance, prevent contamination, and protect product quality in highly regulated manufacturing environments.
-
Explore how ISO 14644 and EU GMP Annex 1 shape cleanroom standards, with a focus on particle control, system accuracy, and the surprising impact of tubing length limitations.
-
Discover how digital integration enhances compliance, streamlines operations, and enables proactive planning for contamination control in pharmaceutical manufacturing
-
Ensure cleanroom air quality with optical particle counters. Explore how OPCs work, their performance metrics, and key considerations for choosing the right one.
-
Examine how counting efficiency and resolution impact data interpretation in critical environments like cleanrooms and pharmaceuticals.
-
Microbiological sampling ensures sterile conditions through surface, passive, and active air methods. The EU GMP Annex 1 emphasizes integrating these for comprehensive environmental monitoring.
-
Airflow visualization studies, crucial for GMP compliance, validate unidirectional airflow effectiveness in contamination control. Discover their enhanced role in quality by design and revised Annex 1 guidelines.
-
Discover how a robust Contamination Control Strategy (CCS) can mitigate contamination risks and gain insights from Ugo Omeronye's detailed responses in our comprehensive reference guide.
-
The new Annex 1 revision emphasizes validation and qualification for sterile drug production. Ensure product quality and contamination control by learning about in-depth requirements for premises and equipment.
WEBINARS
-
Discover how modern strategies like the Contamination Control Strategy are transforming environmental monitoring by exposing hidden risks, enhancing data quality, and unlocking deeper insights through innovative microbial methods.
-
Watch how a single-use microbial impactor revolutionizes contamination control in robotic filling lines to enhance sterility, efficiency, and compliance in fully automated manufacturing environments.
-
Modern environmental monitoring systems are vital for pharmaceutical manufacturing. Explore the benefits of a tool for data collection, analysis, and processing that ensures compliance and adaptability.
-
Annex 1 mandates a risk assessment to identify optimal sample point locations. Explore factors in risk assessment, equipment selection, and system design to maximize data value.
-
There are several factors associated with active environmental microbial monitoring. Watch to learn how the EU GMP Annex 1 compliance focuses on microbial monitoring in cleanrooms.
-
Industry expert Mark Hallworth guides viewers through the latest ISO document (ISO 14644), exploring the reasons behind the decisions made by the team during its development.
-
Airflow visualization techniques like Smoke Studies and CFD analyses are crucial for contamination control, aiding cleanroom qualification, environmental monitoring, and optimizing contamination control strategies under Annex 1.
-
Discover how a Quality by Design approach can streamline the development of new sterile product filling lines, featuring a real-life example illustrating its effectiveness.
-
Discover the importance of compressed gas monitoring in ensuring product quality and compliance with EU GMP standards.
-
Review the standards and regulations promoting a cohesive environmental program, and explore manual compounding in laminar flow hoods, through to filling lines, in both open and closed systems.
-
Gain insight into the standard for microbiological monitoring and control, ISO/EN 17141, and how it harmonizes with ISO 14698 parts one and two.
-
Review the latest revisions to the USP<1788>, which has expanded to support a holistic view of finished product contaminants, how they should be investigated, and added flow imaging technologies.
-
In this webinar we review how to be compliant with the most recent particle counter calibration requirements, particle counter terminology, and how a particle counter works in theory.
-
Modern pharmaceutical manufacturers are already generating and managing big data from environmental monitoring; the next step is to create actionable insights and ensure 21CFR11 compliance. This webinar discusses data collection, 21CFR11 data management and the generation of actionable insights.
-
The New Annex 1 has some critical changes that are important to understand and start applying. While the drafts cover many areas of environmental monitoring in-depth, this webinar by Particle Measuring Systems (PMS) experts focuses on the Viable/Microbial Air Monitoring aspects.
-
Sometimes we focus on data while forgetting how poor practices, bad decisions, incorrect definitions, and lack of evaluations effect the outcome. In this webinar, we analyze how to go from “data” to “data quality” to improve your overall contamination control strategy.
-
Settle plates are a non-validatable method as it is simply based on the physical principle of the downfall of a particle on a surface. We discuss the using active air sampling versus passive air settle plate monitoring in routine environmental monitoring.
-
Defining a Contamination Control Strategy (CCS) is unique for each process and requires an intimate understanding of both the process and how to implement an effective strategy.
PODCASTS
- S2E4: Marc And Mark: Particle Monitoring In Heat Tunnels - Crucial Insights
- Airborne Particle Sampling Techniques
- Manufacturing Contamination Control Strategy And Risk Assessment
- Environmental Risk Assessment: PQ Systems And Tools
- Facility Monitoring Systems (FMS) vs. Building Management Systems (BMS)
- Tackling Viable And Non Viable Isolator Manufacturing
- Continuous Viable Air Monitoring For EU GMP Annex 1
- Risk Assessment When Setting Microbiological Monitoring Conditions
- Working Towards NetZero Emissions In Pharma Manufacturing