Cleanroom solutions and research
CLEANROOM PRODUCTS
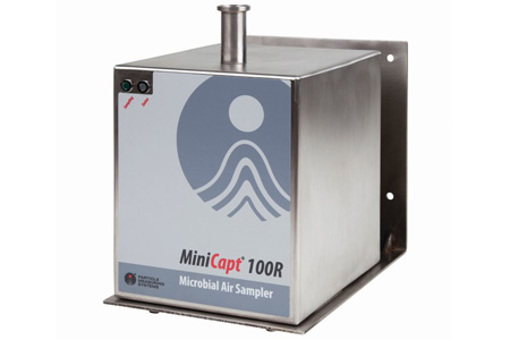
The MiniCapt® Remote Air Sampler features modern, easy to use data and sample configuration management by integration with a FacilityPro® system.
-
Pharmaceutical Airborne Particle Counter: Lasair® Pro
Innovative portable particle counter meeting all regulatory requirements.
-
Biofluorescent Particle Counters — An Environmental Monitoring Solution For Annex 1 And Pharma 4.0
Biofluorescent Particle Counters (BFPC), like the TSI BioTrak® Real-Time Viable Particle Counter, are an alternative microbiological method that serves as the solution for Annex 1 compliance and Pharma 4.0 implementation.
-
AeroTrak™+ Portable Particle Counter A100 Series
Flow Rate 1 CFM (28.3 LPM) - 3.5 CFM (100 LPM) / Channel Sizes 0.3 µm to 10 µm,(6) user selectable channels.
-
Cleanrooms And Equipment For CRISPR Drug Manufacturing
Revolutionizing Gene Editing: Germfree's Pioneering Cleanroom Solutions Propel CRISPR Manufacturing Forward
Cleanroom requirements for CRISPR manufacturing necessitate strict adherence to particulate contamination and operational workflows, ensuring safety and product quality in this transformative field. Germfree’s expertise in providing specialized cleanroom solutions supports the effective production of CRISPR-based technologies and their delivery systems. Germfree provides application based fit-for-purpose facilities design to cater to the unique needs of this rapidly evolving sector.
-
Primary Drug Containers
Oval’s proprietary primary drug containers offer a wide range of benefits over traditional glass based systems. The use of cyclic olefin copolymer (COC) allows for much greater design flexibility, and the creation of more robust containers, whilst also allowing us to remove materials that could potentially interact with the drug. Our COC primary drug container is used as the basis for our platforms ArQ®, ArQ® - Bios and ArQ® - Vita.
-
Cleanrooms And Equipment For Monoclonal Antibodies Manufacturing
Navigating the technical challenges of mAbs production and scalability
Monoclonal antibodies (mAbs) offer promising immunotherapy treatments, targeting antigens and diseases. Manufacturing these complex therapies presents challenges in scaling up, cost, and consistency. Germfree’s expertise in tailored cleanroom solutions addresses these obstacles, ensuring sterility and seamless equipment integration. By providing advanced facilities for both small-scale clinical trials and larger-scale production, Germfree contributes to the successful development and commercialization of mAbs, ultimately improving patient outcomes and transforming healthcare landscapes.
-
Syringe Forming Lines
Syringes are complex products that require an extremely precise forming process: Stevanato Group syringe manufacturing lines include several specifications, which are normally optional, such as servomotors for controlling the most critical manufacturing phases (cone forming, total length) and flow meters for automatically regulating the burners.
-
Rapid Design-Build Cleanroom Solutions: AES Fast-Lane Program
Speed-to-market is the number one driver in the pharma/bio industry today ... the faster our clients can build facilities, the quicker they can get treatments into the hands of the patients who need them the most. The AES Fast Lane program is an accelerated Design, Manufacture, and Installation program that fast tracks your cleanroom facility project in seven months.
-
Optimize Your Contamination Control Strategy
An optimized and effective Contamination Control Strategy (CCS) helps you organization spend less time cleaning and more time manufacturing. Ecolab Life Sciences experts are dedicated to helping you drive the best possible strategy to meet and exceed the GMO Annex 1 CCS requirements.
-
Obtain Temperature Uniformity With An Ultra-Low Temperature Freezer
PHCbi brand's 18.6 cu.ft (528L) ultra-low temperature freezer operates on 220V and features VIP Plus vacuum insulated panels to deliver reliable temperature uniformity throughout the chamber. ENERGY STAR® Certified.
CLEANROOM OVERVIEW
Cleanrooms can be very large. Entire manufacturing facilities can be contained within a cleanroom with factory floors covering thousands of square meters. They are used extensively in semiconductor manufacturing, biotechnology, the life sciences and other fields that are very sensitive to environmental contamination.
The air entering a cleanroom from outside is filtered to exclude dust, and the air inside is constantly recirculated through high-efficiency particulate air (HEPA) and/or ultra-low penetration air (ULPA) filters to remove internally generated contaminants.
Staff enter and leave through airlocks (sometimes including an air shower stage), and wear protective clothing such as hoods, face masks, gloves, boots and coveralls.
Equipment inside the cleanroom is designed to generate minimal air contamination. Only special mops and buckets are used. Cleanroom furniture is designed to produce a minimum of particles and to be easy to clean.
Common materials such as paper, pencils, and fabrics made from natural fibers are often excluded, and alternatives used. Cleanrooms are not sterile (i.e., free of uncontrolled microbes);[3] only airborne particles are controlled. Particle levels are usually tested using a particle counter and microorganisms detected and counted through environmental monitoring methods.[4][5]
Some cleanrooms are kept at a positive pressure so that if there are any leaks, air leaks out of the chamber instead of unfiltered air coming in.
Some cleanroom HVAC systems control the humidity to low levels, such that extra equipment ("ionizers") is necessary to prevent electrostatic discharge (ESD) problems.
Low-level cleanrooms may only require special shoes, with completely smooth soles that do not track in dust or dirt. However, for safety reasons, shoe soles must not create slipping hazards. Access to a cleanroom is usually restricted to those wearing a cleanroom suit.[6]
In cleanrooms in which the standards of air contamination are less rigorous, the entrance to the cleanroom may not have an air shower. There is an anteroom (known as a "gray room"), in which clean-room clothing must be put on, from which a person can walk directly into the room (as seen in the photograph on the right).
Some manufacturing facilities do not use fully classified cleanrooms, but use some cleanroom practices to maintain their contamination requirements.[7][8]
Air flow principles
![]()
Air flow pattern for "Laminar Flow Cleanroom"
|
Cleanrooms maintain particulate-free air through the use of either HEPA or ULPA filters employing laminar or turbulent air flow principles. Laminar, or unidirectional, air flow systems direct filtered air downward in a constant stream towards filters located on walls near the cleanroom floor or through raised perforated floor panels to be recirculated. Laminar air flow systems are typically employed across 80 percent of a cleanroom ceiling to maintain constant air processing. Stainless steel or other non-shed materials are used to construct laminar air flow filters and hoods to prevent excess particles entering the air. Turbulent, or non-unidirectional, air flow uses both laminar air flow hoods and non-specific velocity filters to keep air in a cleanroom in constant motion, although not all in the same direction. The rough air seeks to trap particles that may be in the air and drive them towards the floor, where they enter filters and leave the cleanroom environment.[9]
Cleanroom classifications
Cleanrooms are classified according to the number and size of particles permitted per volume of air. Large numbers like "class 100" or "class 1000" refer to FED-STD-209E, and denote the number of particles of size 0.5 µm or larger permitted per cubic foot of air. The standard also allows interpolation, so it is possible to describe, for example, "class 2000".
A discrete-particle-counting, light-scattering instrument is used to determine the concentration of airborne particles, equal to and larger than the specified sizes, at designated sampling locations.
Small numbers refer to ISO 14644-1 standards, which specify the decimal logarithm of the number of particles 0.1 µm or larger permitted per cubic metre of air. So, for example, an ISO class 5 cleanroom has at most 105 = 100,000 particles per cubic metre.
Both FS 209E and ISO 14644-1 assume log-log relationships between particle size and particle concentration. For that reason, zero particle concentration does not exist. The table locations without entries are non-applicable combinations of particle sizes and cleanliness classes, and should not be read as zero.
Because 1 m3 is approximately 35 ft3, the two standards are mostly equivalent when measuring 0.5 µm particles, although the testing standards differ. Ordinary room air is approximately class 1,000,000 or ISO 9.[10]
US FED STD 209E cleanroom standards
Class | maximum particles/ft3 |
ISO equivalent |
||||
---|---|---|---|---|---|---|
≥0.1 µm | ≥0.2 µm | ≥0.3 µm | ≥0.5 µm | ≥5 µm | ||
1 | 35 | 7.5 | 3 | 1 | 0.007 | ISO 3 |
10 | 350 | 75 | 30 | 10 | 0.07 | ISO 4 |
100 | 3,500 | 750 | 300 | 100 | 0.7 | ISO 5 |
1,000 | 35,000 | 7,500 | 3000 | 1,000 | 7 | ISO 6 |
10,000 | 350,000 | 75,000 | 30,000 | 10,000 | 70 | ISO 7 |
100,000 | 3.5×106 | 750,000 | 300,000 | 100,000 | 700 | ISO 8 |
US FED STD 209E was officially cancelled by the General Services Administration of the US Department of Commerce November 29, 2001,[11][12] but is still widely used.
ISO 14644-1 cleanroom standards
Class | maximum particles/m3 |
FED STD 209E equivalent |
|||||
---|---|---|---|---|---|---|---|
≥0.1 µm | ≥0.2 µm | ≥0.3 µm | ≥0.5 µm | ≥1 µm | ≥5 µm | ||
ISO 1 | 10 | 2.37 | 1.02 | 0.35 | 0.083 | 0.0029 | |
ISO 2 | 100 | 23.7 | 10.2 | 3.5 | 0.83 | 0.029 | |
ISO 3 | 1,000 | 237 | 102 | 35 | 8.3 | 0.29 | Class 1 |
ISO 4 | 10,000 | 2,370 | 1,020 | 352 | 83 | 2.9 | Class 10 |
ISO 5 | 100,000 | 23,700 | 10,200 | 3,520 | 832 | 29 | Class 100 |
ISO 6 | 1.0×106 | 237,000 | 102,000 | 35,200 | 8,320 | 293 | Class 1,000 |
ISO 7 | 1.0×107 | 2.37×106 | 1,020,000 | 352,000 | 83,200 | 2,930 | Class 10,000 |
ISO 8 | 1.0×108 | 2.37×107 | 1.02×107 | 3,520,000 | 832,000 | 29,300 | Class 100,000 |
ISO 9 | 1.0×109 | 2.37×108 | 1.02×108 | 35,200,000 | 8,320,000 | 293,000 | Room air |
BS 5295 cleanroom standards
maximum particles/m3 | ||||||
Class | ≥0.5 µm | ≥1 µm | ≥5 µm | ≥10 µm | ≥25 µm | |
---|---|---|---|---|---|---|
Class 1 | 3,000 | 0 | 0 | 0 | ||
Class 2 | 300,000 | 2,000 | 30 | |||
Class 3 | 1,000,000 | 20,000 | 4,000 | 300 | ||
Class 4 | 200,000 | 40,000 | 4,000 |
BS 5295 Class 1 also requires that the greatest particle present in any sample does not exceed 5 μm.[13]
GMP EU classification
Class | maximum particles/m3[14] | |||
---|---|---|---|---|
At Rest | At Rest | In Operation | In Operation | |
0.5 µm | 5 µm | 0.5 µm | 5 µm | |
Class A | 3,520 | 20 | 3,520 | 20 |
Class B | 3,520 | 29 | 352,000 | 2,900 |
Class C | 352,000 | 2,900 | 3,520,000 | 29,000 |
Class D | 3,520,000 | 29,000 | n/a | n/a |
CLEANROOM WHITEPAPERS AND CASE STUDIES
-
Explore five steps to design an EMPQ for sterile manufacturing: classification, protocol drafting, cleaning evaluation, disinfectant efficacy testing, and continuous improvement.
-
Explore high voltage leak detection, headspace analysis, and vacuum and pressure decay as applied in pharmaceutical manufacturing.
-
The Greenville Water Utility in Indiana is leveraging Qatium to enhance its water management and leak detection capabilities, significantly improving service efficiency.
-
In this paper, we’ll discuss how many companies are losing thousands of dollars each year to compressed air system leaks. We will address where leaks commonly occur, leak detection methods, and practical advice for an audit and repair plan.
-
A mobile cleanroom facility was needed for manufacturing a new monoclonal antibody product for phase 1 clinical trials. The facility had to have the ability to be repurposed for additional applications.
-
Eurofins ensures Annex 1 compliance through robotic isolators, PUPSIT, contamination control strategies, and rigorous training for aseptic sterile fill-finish of early-phase clinical products.
-
A custom hexapod was introduced at ILA Berlin 2024, enhancing precision in aircraft construction. This 6-DOF system improves contour machining of CFRP components, reducing manufacturing times and costs.
-
Clarify HEK293 cells in various stages of production from research to manufacturing with a family of products that demonstrate high yield and viability rates while maintaining target NTU readings.
-
Aseptic processing is evolving. Regulatory changes and technological advancements are driving a shift from open cleanrooms to closed systems for sterile drug manufacturing.
-
Filtration removes contaminants to ensure safety and is essential in various applications, from lab-scale tasks to GMP production. Explore how its simplicity and reliability make it indispensable.
-
Discover how a successful partnership between an environmental company and a liquid storage facility helped mitigate a disaster from escalating and gave them the rapid response they needed.
-
Read about a non-invasive and non-intrusive technology that enables rapid inspection of large areas of a water distribution network without removing the pipelines from service, avoiding service interruptions, pipeline dewatering/cleaning, or costly excavations.
-
Read about a 5-module ABSL-3 facility that was constructed in Singapore, and is used for disease surveillance, research on avian influenza, and other risk group 3 materials.
-
Uncover how Germfree designed and installed a mobile cGMP cleanroom on a 53′ tractor-trailer chassis to provide a flexible and efficient cleanroom solution tailored to the company’s needs.