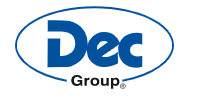
ABOUT DEC GROUP
Headquartered in Switzerland, Dec Group is a distinguished global leader in delivering integrated process solutions tailored for a variety of industries, with a strong focus on the chemical and pharmaceutical sectors. Their unwavering commitment to safety ensures that their products prioritize the well-being of operators while safeguarding the integrity of the materials they handle.
As pioneers in advanced system concepts, Dec Group provides a comprehensive range of solutions, from standard powder transfer systems to sophisticated, fully integrated handling and processing equipment. Their innovative systems not only boost productivity but also comply with the latest regulatory standards, offering customers peace of mind and confidence in their operations.
Dec Group has experienced significant growth through strategic acquisitions and now offers a wide range of products in five divisions: Powder Handling, Particle Size Reduction, Filling Solutions, Containment Solutions, and Continuous Processing Technologies. The group's comprehensive solutions ensure seamless integration and high quality from raw material input to final dosage form.
CONTACT INFORMATION
Dec Group
1118 Industrial Pkwy.
Brick, NJ 08724
UNITED STATES
Phone: +1 (848) 448-2829
Contact: Frederic Pasche
FEATURED ARTICLES
-
Explore a comparative analysis that showcases the superior performance of continuous processing over traditional batch methods, highlighting key improvements in efficiency and environmental impact.
-
Adopted by leading chemical and pharmaceutical firms, MTP-based ACPP aligns with industry standards, offering portable, easily integrated solutions for continuous, efficient API production needs.
-
Reveal how one pharmaceutical facility overcame strict cross-contamination rules and space limits without costly building modifications to ensure operational continuity.
-
Dec Group is pleased to announce a significant expansion project that will double the manufacturing capacity at its Mauston, Wisconsin facility. This location serves as a full-cycle manufacturing hub for the Dec Group in North America and is one of the two operational sites in the United States.
-
Dec Group, a global leader in aseptic and high containment processing solutions, is pleased to announce the acquisition of the activities of BAUSCH Germany GmbH.
-
Risk assessment is integral to manufacturing processes, particularly in drug production, and having effective containment strategies can help identify potential hazards and ensure worker safety.
-
Explore how understanding the transport phenomenon in the boundary layer can allow us to engineer the flow to manage the rate-limiting step and intensify the process.
-
Aseptic filling technology is of utmost importance. Explore in great detail an aseptic filling solution that has been specifically designed for laboratory and R&D applications in the pharmaceutical industry.
-
The Dec Group is running an informative webinar series through 2023 on various impactful topics across our industry. Various subject matter experts each with many years of in-industry experience in their chosen field will recount challenges presented in actual projects and processes and how they were overcome in each event. Keep an eye out each month for the next webinar session, held on the 3rd week of each month to the end of the year.
-
Dual-chamber syringes (DCSs) are in high demand across the pharmaceutical and hospital industries. Learn about the challenges of the DCS filling manufacturing market and how to overcome them.
-
Recently, Dec Group has successfully implemented a fully automated Blood Bag Processing System (BBPS) at Sanquin, a not-for-profit based organization responsible for the safe and efficient blood supply in the Netherlands.
-
Powder handling and process specialist Dec Group will show innovative flow chemistry solutions with recently acquired UK-based Alconbury Watson (AWL) and various handling and processing technologies at the ACHEMA 2022 expo held in Frankfurt from August 22 - 26.
-
We are very pleased to announce the recent acquisition of UK-Stoke-on-Trent based AWL, one of the most dedicated companies for the design, manufacture and supply of continuous processing technologies and systems. Over the past decade, they have translated the much-debated ideas of continuous processing into reality for current use in the chemical, food and pharmaceutical industries by offering solutions from laboratory evaluation systems to production scale turnkey systems.
-
Extract Technology and the Dec Group (Dietrich Engineering Consultants) announce a significant expansion of their UK ISO 9001 manufacturing facility located in Huddersfield, UK. The Bradley Junction site expansion includes the acquisition of an additional building within the current industrial complex.
-
Here, we address a number of OHS, regulatory, and process requirements imperative to the delivery of critical containment systems.
-
Gain insight into how a customized aseptic processing need was met for the safe processing of irreplaceable personalized T-cell therapies.
-
Extract Technology and the Dec Group announce production expansion to existing Midwest, USA operations! Extract’s New Lisbon, WI manufacturing operations will see expansion to a new, renovated Midwest site in neighboring Mauston, WI. The facility and investment provides a fantastic opportunity for optimizing manufacturing layout, capital equipment upgrades and creating a customer focused environment with potential for future expansion as we grow the Dec Group and Extract businesses.
-
The earliest uses of aseptic isolators were for sterility testing. Sterility test isolators make up most of the aseptic isolators in use and are available in many different sizes and configurations.
-
Earlier today, The Dec Group completed the acquisition of the Extract Technology business from US based Wabash National Corporation, a US listed company (NYSE: WNC).
-
Powder handling and high containment specialists Dec Group has announced the appointment of Intrepid Bioprocess Technologies as their US agent for the Westcoast including California, Oregon and Washington.
-
Although most legislation concerning the traceability of pharma products focuses on serialization rather than aggregation, the latter is an essential component of internal and external traceability of products.
-
Pharmaceutical manufacturing staff, equipment, and premises are all subject to stringent quality controls. Read about the latest status, trends, and technologies in parenteral filling equipment.
-
Dec will participate in the 2020 PDA Universe of Pre-Filled Syringes and Injection Devices event held October 5 – 8. This year's conference will be held virtually. It offers industry expertise by sharing new developments and trends in this continuously growing market while also reflecting on regulatory matters and common challenges.
-
Over more than three decades, Dec Group has brought innovation to the pharmaceutical process industry by introducing active versus gravity charging and process linking with its Powder Transfer System (PTS), a unique solution that uses both pressure and vacuum to ensure all forms of dry powders and granules flow efficiently and safely between processes and containers.
-
A customer had planned a new facility for the production of intravenous liquids. They were facing a challenge of charging multiple vessels with salt, glucose and active carbon under controlled conditions achieving high accuracy. See what solution allowed them to create a highly automated high capacity facility.
-
A facility handled sterile blending and packing powder from a tilting filter dryer under sterile conditions. They were transferring the discharge of the tilting dryer by screw feeder and transferring into an agitated mixer. Discharging the mixer by a screw feeder into a packing system. They were encountering sterility loss through mechanical seals and docking of the dryer to the screw feeder and difficulties to clean and sterilize the system in place. A solution was a full automatice system including a transfer system, batchmixer and sampling device.
-
An operation required manual filling of IBCs by using a flexible isolator installed on an upper floor with large amounts of excipients (lactose and micro cellulose)> 100 kg and only a small amount of APls of a few kilos. Operation was strenuous due to the large quantity of excipients to be handled in the isolator which lead to the damage of the flexible isolator and containment breach. Several equipment and process changes allowed them to see an increase of plant productivity.
-
A multipurpose facility for API production had various requirements including milling, micronizing, packaging, and the possibility to blend various batches together before or after milling.
-
By reviewing and evaluating the health and safety data for each product involved in the manufacturing process this supplier was able to determine that the correct containment solution.
-
Cell and gene therapies are currently produced in fixed facilities that require a significant upfront investment. Modular concepts offer an opportunity to shift from these large, fixed assets.
-
The move from sterility testing within LAF safety cabinets to those in aseptic isolators has resulted in a marked decrease in false positives.
-
To allow a pharma facility to maintain regulatory compliance with ISO 5 conditions ensuring product protection, a positive to ambient pressure regime was used within the airlocks.
-
Advancements in Pharma 4.0 are driving the need for facility design solutions to deliver cost savings. Learn why integrating closed processes is an increasingly effective method for efficiency.
-
Uses of isolators for aseptic processing are far reaching. The earliest use of aseptic isolators were for sterility testing. Sterility test isolators make up most of aseptic isolator use and are available in many different sizes and configurations.
-
Due to the high potency of APIs, machine operators must be protected. Yet, humans are a high source of product contamination. In pharma manufacturing facilities, isolators are becoming increasingly important.
-
As isolators become more customized to meet the requirements of specific Pharmaceutical processes, the controls systems have been challenged to provide more safety and flexibility.
-
Learn about the critical changes in the Annex 1 guidance from a process equipment provider's perspective, several areas where process and product change could take place, and more.
-
These days several Pharmaceutical companies are moving to single use, flexible film isolators for containment of potent compounds during Pharmaceutical processing. Flexible film isolators have also been used for aseptic processes, like sterility testing.
-
While price is certainly an important reason for buying any piece of capital equipment, it is not always the top reason. There are important considerations to examine when selecting an isolator supplier.
-
The mobile clean room is a self-contained manufacturing space fully constructed off-site. It is shipped to customer facility on a double drop flatbed trailer in one piece and ready to hook up.
-
Achieving high performance with conventional jet mills remains very difficult. Read about a new generation of spiral jet mills meeting specific particle size distribution targets that have been developed.
BROCHURES
- Pharmaceutical Labeling Equipment: DecFill® LM-200
- Disposable Pump Tube Kits
- Rotary Piston Pumps
- Automatic Vial Tray Loader: DecFill® TL-1200/2400
- Plunger Rod Assembly Machine: DecFill® SA-150
- Automatic Labeling Machine: DecFill® LM-560
- High Speed Vial Filling Machine: DecFill® HVF-200, 400, 600
- Nested Syringe Filling Machine: DecFill® nSF-1
- Vial Filling And Closing Machine: DecFill® VF-2
- Semi-Automatic Rotary Piston Pump: DecFill® LAB-mRP
- Semi-Automatic IV Bag Filler: DecFill® LAB-IV-2/4
- IV Bag Filling And Closing Machine: DecFill® IV
- Rotary Filling And Closing Machine: DecFill® mRF-60
- Ampoule Filling And Closing Machines: DecFill® AF-200-400
- DecFill® STU Sterilization Tunnel
- Rotary Washing Machine: DecFill® RW-200
- DEC Aseptic Butterfly Valve
- Advanced Configurable Process Plant – Extraction Booth
- Containment Solution Technologies
- Aseptic Filling Solutions
- Overcoming Aseptic Manufacturing Challenges To Prevent Contamination
- 10 Advantages Of MC DecJet® Micronization
- Mobile Clean Room Solutions
- Pharmaceutical Packaging Serialization Integration Partner
- Pharmaceutical Packaging Serialization Equipment
- Pharmaceutical Packaging Item Serialization Units
- Pharmaceutical Packaging Case Serialization Units
- Lyophilization (Un)Loading Equipment Solutions
- Primary Packaging Filling Lines And Containment Units
- Transbatch Transfer System With High Containment Vacuum And Pressure
- Suction Hoppers
- Single Charge Container - Small Powder Charging
- SafeDock - Connection And Containment System
- Safe Handling Of Toxic And Corrosive Liquids
- R&D Micronizer MC DecJet 30®
- PTS Powder Transfer System® CIP SIP Hygienic Design
- PTS Powder Transfer System
- PTS Powder Transfer System Mobile Version
- PTS Batchmixer High Containment Powder Mixer
- Production Scale Micronizer MC DecJet® 200
- Powderflex - Combined System For Conveying And Dosing Powders
- Pilot Scale Micronizer MC DecJet® 150
- Pilot Scale Micronizer MC DecJet® 100
- Packing Of High Potent APIs
- MPTS - Safe Sampling Of Toxic Or Explosive Powders
- MC DecJet® 300 Production Jet Mill
- MC DecJet® 50 Jet Mill Micronizer
- MC DecJet 400 Micronizer, Micronizing Up To 300 kg
- Lump Breaker Suction Lance
- Isotube - High Containment Drum Emptying
VIDEOS/WEBINARS
-
Imagine a future where personalized medicine isn't a luxury, but a reality. Where cutting-edge digital advancements revolutionize the way we deliver care, making it accessible to all.
-
Gain insight into the proper timeline for process validation, the importance of linking the User Requirements Specification (URS) to each step of validation to ensure complete compliance, and more.
-
A fully automated Blood Bag Processing System (BBPS) a Dutch blood supply organization is completely tailor-made with an ergonomic design custom-made to the workflow requirements of the blood bank.
-
This video highlights Dec’s high containment micronizing technology and materials handling systems. See how a complex two-floor large scale high containment micronizing plant equipped with fully contained sampling and pack-off technology solutions ensure OEL levels are kept well under the target while allowing fully streamlined processes.
-
Dec Group is your partner in powder handling and process contamination technologies. With locations around the globe we have over 30 year of experience in contained and sterile powder handling solutions. This video highlights our capabilities and our state-of-the-art solutions for sophisticated risk management.- Dec Group is your partner in powder handling and process contamination technologies. With locations around the globe we have over 30 year of experience in contained and sterile powder handling solutions. This video highlights our capabilities and our state-of-the-art solutions for sophisticated risk management.